Why Automation is the Future of Work Order Management for Utilities
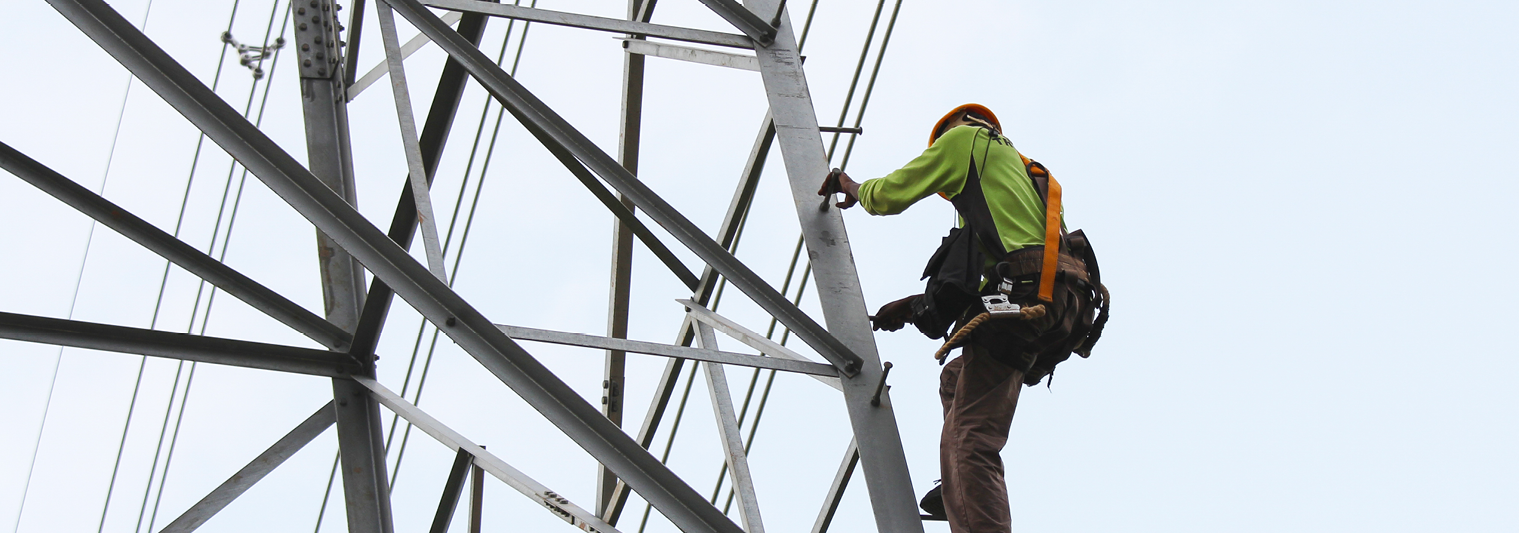
Sweeping change has taken hold of the utilities industry. Robotic process automation is profoundly changing the relationship that utility field service personnel have with smart assets.
Organizations around the globe integrate automation into their operations and results have been promising. According to Capgemini Research Institute’s Intelligent Automation in Energy and Utilities survey, utility companies that have deployed intelligent automation at scale expect to save from $237 to $813 billion.
Despite this, the survey also found that nearly half of utility companies have underestimated the benefits derived from intelligent automation initiatives, with only 18% deploying use cases and 17% deploying use cases at scale.
Productivity levels are bound to increase with automation, and this can benefit utility workers and companies. For example, autonomous platforms can be deployed to power generation to regulate generation in a power plant. Through intelligent automation, utility field operators can also deal with fluctuation in wind turbine repair and maintenance processes.
With Industry 5.0 closer than we think, the rise of automation signals the need for a seamlessly connected workforce to achieve desirable outcomes.
Innovapptive’s enterprise asset management (EAM), field services, inventory and supply chain management solutions provide access to real-time and mission-critical data. Through automation and mobilization, real-time data connects utility field-level workers to back-office systems to executives, creating total operational visibility.
Work order management teams can leverage Innovapptive’s mobile work order management (mWorkOrder) application to achieve full visibility and collaborate effectively with field technicians. Automation and mobilization technologies delivered by Innovapptive makes this possible. By automating work order process, technicians get full access to work order scope to review histories and study critical asset information for speedy repair and effective maintenance work.
There’s no question about automation whether or not it be instrumental for the success of the utilities of the future, but instead just about how much.
As you evaluate and invest in disruptive technologies for your utility business, you can download our Conversational Operations Accelerate Digital Utilities Transformation white paper here to learn more about the path of automation.
Innovapptive is a top-tier software provider confidently leading the world’s largest brands in oil & gas, utilities, chemicals, mining, and manufacturing into the digital revolution. Its mission is simple: innovate, transform and empower. Innovapptive is a partner of SAP, IBM, IBM® Maximo, Atos, CRITIGEN, we-do-IT, Honeywell, Zebra Technologies and Cognex.
Want to Discover More?
Innovapptive – a Connected Worker Platform provider – has a simple mission: “Connect and create conversations between people, machinery and work processes while improving people’s lives.” Innovapptive offers the only Connected Worker Platform that digitizes the last mile of your front-line workers into SAP and IBM (watch a short video here). We’d like to show how our Connected Worker Platform and related applications can help you successfully start and complete your journey to more efficient, safe and productive plant operations. Schedule a free demo today by calling 844-464-6668 or or by clicking here.
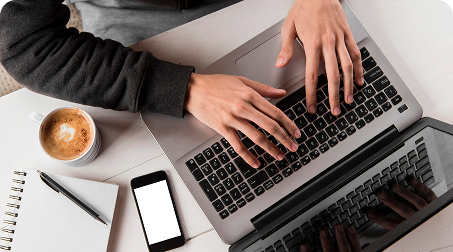
See It In Action
Schedule a personalized demo to see how our solutions can help your business thrive.
- 20-08-2025
Building the future of Industrial Operations with Innovapptive and AWS
Most manufacturers have already gone digital. Yet business outcomes haven’t moved in step. Many...
- 22-04-2025
The $3.6B Unlock: Solving the Chemical Industry’s Labor Crisis and EBITDA Pressure in One Move
“Constraints don’t slow innovation—they force it.”
- 21-04-2025
Chemical Industry's Margin Erosion: A Wake-Up Call for Operational Efficiency Amid China's Oversupply
The global chemical industry is facing mounting challenges, with revenue declines and shrinking...