Mobile Operator Rounds Solution for Chemical Manufacturing
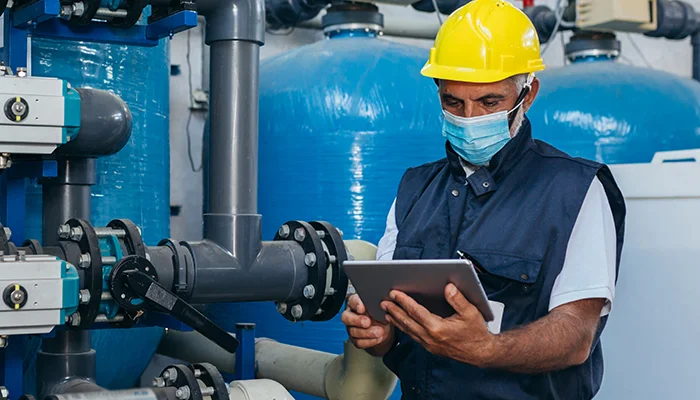
In the rapidly evolving era of Industry 4.0, the chemical manufacturing sector, known for its complexity and high safety demands, is actively adopting innovative solutions to modernize and optimize its operations. A crucial aspect of this transformation is the digitization of operator rounds, which are vital for maintaining equipment efficiency, ensuring continuous production, and adhering to stringent safety and environmental regulations. Innovapptive's mobile operator rounds solution marks a significant advancement in this area, offering real-time data access and digital tools that enhance efficiency, safety, and regulatory compliance in chemical manufacturing.
Challenges of Traditional Methods in Chemical Manufacturing
In the chemical industry, traditional operator rounds, which largely depend on manual paperwork, present numerous challenges. This reliance on antiquated processes results in delayed and inaccurate information, severely impeding effective decision-making. These inefficiencies can affect production and complicate maintenance operations. Moreover, the hazardous nature of chemical manufacturing, often involving volatile materials and stringent environmental conditions, calls for more agile and responsive approaches for equipment maintenance and safety management. The persistence of these conventional methods significantly exacerbates these challenges, highlighting the need for more advanced, efficient operational solutions.
Major Challenges of Traditional Methods:
- Dependence on Paperwork: Traditional methods often rely on manual record-keeping, leading to information delays and inaccuracies.
- Delayed Decision-Making: The absence of real-time data hinders prompt and effective decision-making, essential in the dynamic environment of chemical manufacturing.
- Operational Inefficiencies: Outdated processes contribute to inefficiencies in production and maintenance operations.
- Safety and Maintenance Complexities: The demanding conditions in chemical manufacturing require robust safety measures and equipment maintenance, often hindered by conventional methods.
- Need for Modernization: These traditional approaches underscore an urgent need for more sophisticated, efficient operational solutions.
The Impact of Downtime in Chemical Manufacturing
Equipment failure in chemical manufacturing can have significant financial and safety implications. A typical chemical plant allocates a substantial portion of its annual expenditure to asset maintenance and repairs. Downtime, even for an hour, can cost a considerable amount, leading to substantial losses per incident.
The Importance of Mobile Operator Rounds in Chemical Manufacturing
The adoption of mobile operator rounds in chemical manufacturing is becoming increasingly vital due to several key factors:
- Enhanced Real-Time Data Access: Mobile solutions offer instant access to operational data, enabling quicker, more informed decision-making.
- Increased Efficiency: By replacing manual, paper-based processes, mobile rounds streamline operations, reducing time and resource wastage.
- Improved Safety and Compliance: Real-time monitoring and reporting capabilities enhance safety standards and ensure environmental and regulatory compliance.
- Cost Reduction: Reducing downtime and maintenance costs through proactive issue identification and resolution.
- Data Accuracy and Quality: Digital tools provide more accurate and comprehensive data collection, improving overall operational insights.
Innovapptive’s Mobile Operator Rounds Solution: Transforming Chemical Manufacturing
Innovapptive's mobile operator rounds solution, mRounds, is designed to empower operators with real-time field data, enabling streamlined operations, enhanced efficiency, and increased productivity in chemical manufacturing. This solution aids in improving safety, reducing downtime, and enhancing compliance.
Key Features:
- Real-Time Data and Visibility: Eliminate inefficient paper-based data collection for real-time tracking and decision-making.
- Drag and Drop Rounds Builder: Create and modify rounds templates easily for consistency and standardization.
- Integrated Shift Turnover: Smoothens transition between shifts, enhancing productivity and reducing communication gaps.
- Operator Shift Logs: Document actions, tasks, and observations for compliance and continuous improvement.
- Work Notification Entry: Enable prompt issue resolution with field-based work notification entry.
- Predictive Rounds: Integrate with Asset Performance Management solutions for proactive issue identification.
- Digitize Rounds Planning: Tools for creating detailed operator rounds plans and routes without paperwork.
- Application in Various Chemical Manufacturing Settings: Suitable for different types of chemical plants, the solution helps in identifying and resolving safety and equipment concerns efficiently.
The transition to mobile operator rounds is a pivotal step for the chemical manufacturing industry in its journey towards digital transformation. Innovapptive's mRounds platform stands as a comprehensive solution, addressing critical aspects of chemical manufacturing operations from safety to efficiency and compliance.
To discover how Innovapptive's solution can revolutionize your chemical manufacturing operations, schedule a free demo today. For a deeper understanding of this technology's capabilities,watch this informative video.
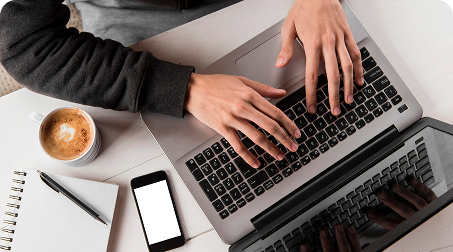
See It In Action
Schedule a personalized demo to see how our solutions can help your business thrive.
- 22-04-2025
The $3.6B Unlock: Solving the Chemical Industry’s Labor Crisis and EBITDA Pressure in One Move
“Constraints don’t slow innovation—they force it.”
- 21-04-2025
Chemical Industry's Margin Erosion: A Wake-Up Call for Operational Efficiency Amid China's Oversupply
The global chemical industry is facing mounting challenges, with revenue declines and shrinking...
- 21-04-2025
Why Wrench Time Isn’t Improving: The Hidden Costs of Traditional Maintenance Scheduling
For years, industrial leaders have relied on a common but flawed assumption: "Better planning and...