5 Strategies That Help Manufacturers Eliminate Work Order Backlogs
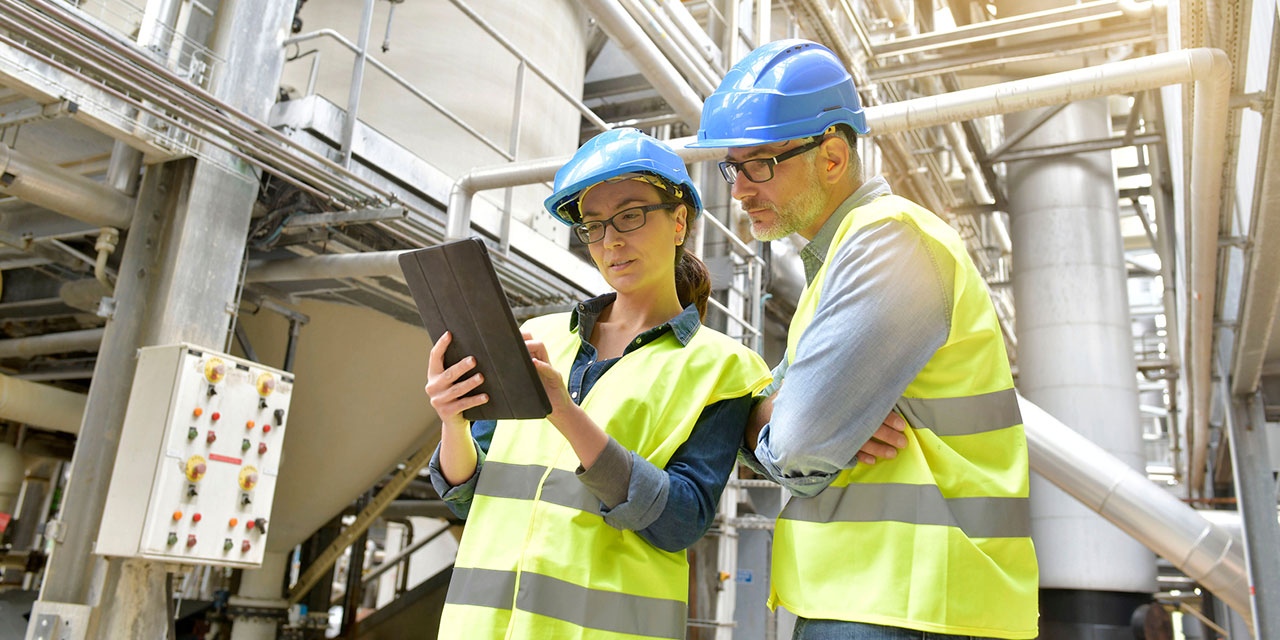
Schedule slippage and downtime speak to the high-cost and high-risk nature of the asset intensive industries. These key operational challenges in the asset intensive industries are primarily caused by large maintenance work order backlogs that are brought about by inefficient plant and equipment maintenance.
A joint study by Wall Street Journal and Emerson revealed that unplanned downtime has cost manufacturers nearly $50 billion annually, with asset failure as the primary cause of 42% of this downtime.
Here are the top five strategies we identified for an effective plant and equipment maintenance to eliminate work order backlogs and meet today’s high-pressure production schedules:
1. Give maintenance engineers a voice
Maintenance teams arrive with very little input when buying new parts or equipment. This is because they are often left out in the decision-making process. Your maintenance team knows the plant inside and out, and it is only sensible for them to have a say in the ongoing maintenance of production line machinery and equipment.
2. Embrace an advanced, digital maintenance management practice
It is no longer efficient to rely on paper reports. Bid goodbye to inefficient manual and paper-based plant maintenance processes. The constant reliance on manual, paper-based processes not only result in data inaccuracy but also in long hours of wasted time by workers in data collection instead of actual inspection and maintenance of equipment. What is beneficial is predictive maintenance that helps you eliminate risk by providing you with real-time access and data capture capabilities.
3. Incorporate real-time AI-powered data analytics
The price of unplanned downtime could be higher than a smart maintenance system. Move away from reactive maintenance to proactive systems by leveraging AI-based solutions that provide you the capability to track subtle abnormalities as well as predict the next failure of a part, machine or system.
4. Improve user experience across the team
The most effective approach to reducing risk and eliminating work order backlogs in manufacturing is by empowering your workforce with the proper resources. Do this through an end-to-end digital transformation of equipment and plant maintenance that provides your plant technicians, operators and craft workers with a real-time enterprise asset management (EAM) solution. Innovapptive offers mWorkorder and RACE Dynamic Inspection Forms, a plant and equipment solution, that delivers an intuitive user experience leading to the seamless collaboration of plant supervisors, back-office staff, plant managers, warehouse managers and operational executives by ensuring everyone is equipped with the data and analytics needed in important decision-making processes.
5. Streamline and expedite inspections process
Implement a digital platform that will allow you to converge the latest technology trends such as IoT, AI, machine learning, drones and mobile technology. To help optimize and streamline pipeline inspections, Innovapptive also offers RACE™ Dynamic Forms, a solution that enables pipeline companies to eliminate paper trails, convert error-prone inspection process with digital forms and improve the data collection process. With powerful automation and real-time access to submitted data, this solution not only improves accuracy but also delivers significant cost and time savings.
Find out how you can see instant value with a high-performance mobile work order solution.
Frequently Asked Questions (FAQs)
1. What causes work order backlogs in manufacturing?
Work order backlogs result from inefficient scheduling, lack of visibility, delayed approvals, and reliance on paper-based processes, leading to downtime and production delays.
2. How can involving maintenance engineers help reduce work order backlogs?
Involving maintenance engineers in proactive planning and real-time tracking improves task prioritization, speeds up execution, and reduces backlogs.
3. What challenges do paper-based maintenance processes create for manufacturers?
Paper-based processes cause delays, miscommunication, and tracking errors, leading to increased work order backlogs and unplanned downtime.
4. How do work order backlogs impact production schedules and downtime?
Backlogs disrupt production schedules, delay repairs, increase downtime, and raise operational costs.
5. How does digital maintenance management help eliminate work order backlogs?
Digital maintenance management automates scheduling, tracks work orders in real-time, and improves team communication, reducing delays and bottlenecks.
6. What technologies are most effective in streamlining work order processes?
Mobile work order management, IoT-enabled predictive maintenance, AI-driven analytics, and cloud-based CMMS optimize workflows and minimize delays.
7. How to reduce manufacturing backlog?
Implement digital work order management, automate preventive maintenance, and prioritize tasks to improve efficiency and eliminate backlogs.
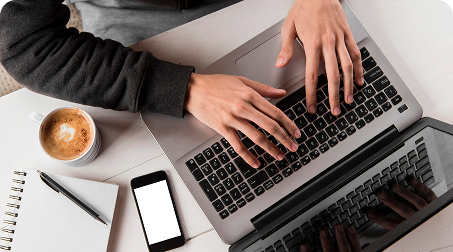
See It In Action
Schedule a personalized demo to see how our solutions can help your business thrive.
- 20-08-2025
Building the future of Industrial Operations with Innovapptive and AWS
Most manufacturers have already gone digital. Yet business outcomes haven’t moved in step. Many...
- 22-04-2025
The $3.6B Unlock: Solving the Chemical Industry’s Labor Crisis and EBITDA Pressure in One Move
“Constraints don’t slow innovation—they force it.”
- 21-04-2025
Chemical Industry's Margin Erosion: A Wake-Up Call for Operational Efficiency Amid China's Oversupply
The global chemical industry is facing mounting challenges, with revenue declines and shrinking...