Optimize Your Plant’s MRO Program with a Connected Worker Platform
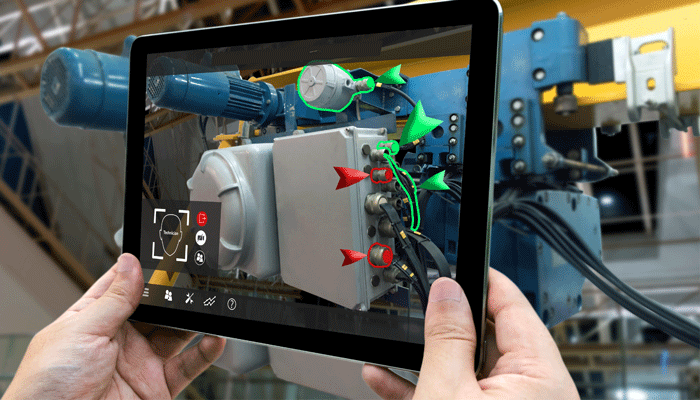
Are you spending more than 5 percent of your asset’s value on MRO (Maintenance, Repair, and Operations) each year? If yes, you should optimize your plant’s maintenance operations while achieving high equipment uptime. If you are wondering how, read on this blog post to explore how Connected Worker technologies can help you.
A Connected Worker Platform to Optimize MRO
A Connected Worker Platform eliminates slow, inefficient paper-based data collection and replaces it with real-time data capture and distribution. Front-line workers can connect with remote experts on-demand via two-way video conferencing that delivers a “see-what-I-see” experience. This digital process encourages greater communication between front-line workers, managers and back-office systems, such as SAP and IBM Maximo. Information silos disappear. Leaders have access to immediate data to make knowledgeable decisions. This helps them address maintenance issues before they become downtime-causing problems.
Front-line workers can access the equipment maintenance history, look up bills of materials hierarchy, availability of spare parts and then receive step by step, visual and guided work instructions on mobile or wearables. This enables a “hands-free” operation to close jobs faster. These connected worker experiences are then turned into insights for executives, directors, managers and supervisors to reimagine their maintenance programs. A best-in-class Mobile Plant Maintenance app can transform a slow, reactive program into an efficient, proactive one that reduces downtime and increases production capacity.
This transformative maintenance automation solution is guided, intuitive and digitizes operational data. Users can seamlessly integrate SAP/IBM Maximo operational data with front- line worker work instructions, SOPs and more. Best-in-class platforms and pre-packaged apps are also agile and reconfigurable. This personalization allows users to rapidly respond to changing business and regulatory conditions. This easy-to-use platform empowers front-line workers and managers to collaborate and share data anywhere, at any time, enterprise-wide.
Redefining Work Order Management
A best-in-class Connected Worker platform should support the creation of configurable digital SOPs, work instructions, risk assessments and checklists. Technicians and inspectors should no longer perform operator rounds using paper forms, clumsy clipboards or heavy binders. Instead, managers and supervisors can quickly create digital work instructions, SOPs, and data capture forms with customizable fields to fit your unique operational requirements. Techs and inspectors are armed with mobile devices such as smartphones, tablets and smart glasses to complete these operations and visual and guided, step-by-step work instructions, SOPs and digital checklists that can ingest the data in real-time. Decision-makers can follow the operator rounds and risk assessments via their own mobile device or through a desktop application. They’ll immediately know when an issue is found and can take corrective action much faster than through the old paper-based processes. Decision makers can address problems before they cause costly downtime, resulting in a safety issue or become a regulatory compliance concern.
Prioritize maintenance work orders based on the risk profile of all equipment throughout your plant:
● Use risk information to prioritize push notifications and work orders,
● Rank issues based on problem severity, likelihood and duration, or the criteria of your choice,
● Embed risk and safety measures information in the work order’s safety plan section.
By empowering maintenance teams with real-time data, guided work instructions, and elimination of manual processes and human errors, a best-in-class Connected Worker platform reimagines and transforms maintenance operations to reduce costs and maintain high equipment uptime.
Want to Learn More?
Discover how a best-in-class Connected Worker platform optimizes your MRO program through a customized, live demo of Innovapptive’s Mobile Plant Maintenance application: For more information, visit www.innovapptive.com or call 1-844-464-6668 to talk to an expert.
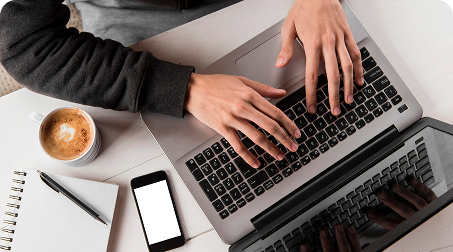
See It In Action
Schedule a personalized demo to see how our solutions can help your business thrive.
- 20-08-2025
Building the future of Industrial Operations with Innovapptive and AWS
Most manufacturers have already gone digital. Yet business outcomes haven’t moved in step. Many...
- 22-04-2025
The $3.6B Unlock: Solving the Chemical Industry’s Labor Crisis and EBITDA Pressure in One Move
“Constraints don’t slow innovation—they force it.”
- 21-04-2025
Chemical Industry's Margin Erosion: A Wake-Up Call for Operational Efficiency Amid China's Oversupply
The global chemical industry is facing mounting challenges, with revenue declines and shrinking...