Enhance Your Chemical Plant Safety and Equipment Reliability through Mobile Operator Rounds
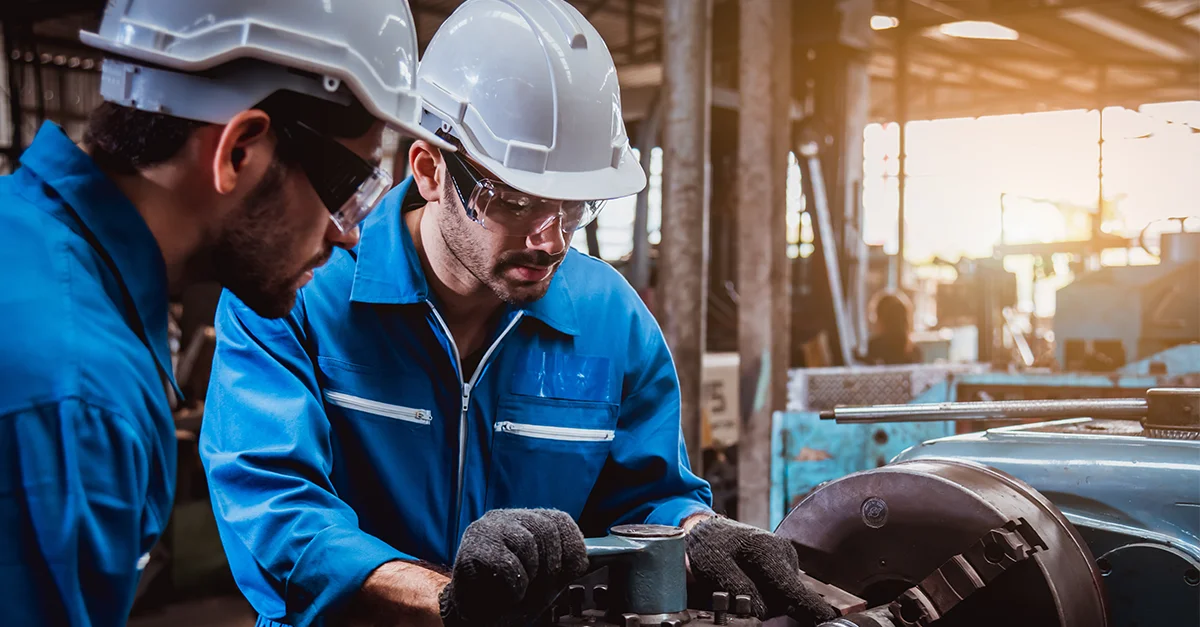
Chemical plant downtime costs the industry an average of $20 billion a year. Mobile operator rounds can cut costly unplanned downtime while improving chemical plant safety by giving decision-makers real-time data to take prompt remedial action.
The Critical Role of Mobile Operator Rounds in Enhancing Plant Safety
A survey finds that 88% of accidents in the chemical industry stem from the release of toxic chemicals. Inefficient maintenance of storage tanks, pumps, and other critical equipment causes such incidents. Enhancing operator rounds is critical to strengthening equipment maintenance. But will mobile operator round solutions help you optimize the process?
Challenges Facing Chemical Operators Rounds
Working with chemical equipment like vacuum pans and mixers is inherently risky. For instance, a hazardous gas leak can endanger lives, harm the environment, and halt operations. Take the recent Vizag gas tragedy killed 11 people and impacted thousands of lives due to a leak in a storage tank after a 40-day shutdown.
Performing operator rounds effectively can help companies prevent such catastrophic incidents. However, many chemical companies still rely on paper-based forms for inspections. These outdated methods create several problems:
- Inefficient inspections
- Delayed reporting of safety risks
- Increased operational costs
- Productivity and revenue losses
- Potential fines for non-compliance
An operator round inspection needs to be thorough and real-time to be effective. Unfortunately, static paper checklists fall short of meeting this requirement. They are inflexible, prone to incomplete reporting, and incapable of offering real-time visibility into safety conditions.
Leveraging Mobile Operator Rounds Solutions
Mobile operator round solutions replace paper forms with digital checklists accessed on smartphones, tablets, or wearable devices. These solutions offer flexibility and real-time benefits:
- Dynamic Forms: Unlike static paper checklists, digital forms can be updated instantly to reflect operational changes.
- Real-Time Data: Technicians can upload inspection data directly into systems like SAP or other enterprise resource planning (ERP) platforms, enabling instant visibility for decision-makers.
- Enhanced Collaboration: Technicians and decision-makers can collaborate in real-time, ensuring risks are mitigated promptly.
For example, technicians can:
- Scan equipment barcodes for faster data input.
- Use customized fields to record equipment status, safety conditions, or operational parameters.
- Share live inspection results with management to guide immediate actions.
This seamless data flow ensures critical issues like natural gas leaks, equipment malfunctions, or fire risks are identified and addressed promptly.
The Benefits of Mobile Operator Rounds
By adopting mobile operator rounds, chemical plants can overcome key challenges, including:
- Lack of Real-Time Data Visibility: Decision-makers can now monitor plant operations remotely.
- Data Quality Issues: Digital inputs eliminate manual errors and ensure accurate reporting.
- Risk Modeling: With reliable data, plants can better predict and mitigate risks related to safety and efficiency.
- Enhanced Compliance: Maintain operational standards and regulatory compliance seamlessly.
Enrich Operations Efficiency and Safety
Switching to mobile operator rounds boosts operations efficiency by reducing downtime and optimizing inspection workflows. This translates into improved plant performance, higher reliability, and a safer working environment. By leveraging real-time data, chemical plants can stay ahead of potential risks, including the threat of plant fires.
Want to Learn More about Mobile Operator Rounds?
Our experts are always happy to help you learn more about mobile operator rounds solutions and how it helps your chemical company? Schedule a free demo today or call us at 844-464-6668.
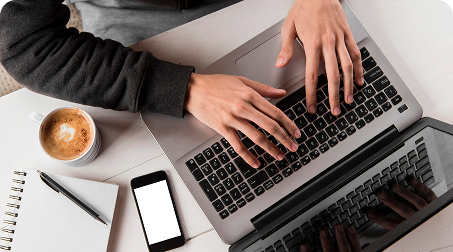
See It In Action
Schedule a personalized demo to see how our solutions can help your business thrive.
- 22-04-2025
The $3.6B Unlock: Solving the Chemical Industry’s Labor Crisis and EBITDA Pressure in One Move
“Constraints don’t slow innovation—they force it.”
- 21-04-2025
Chemical Industry's Margin Erosion: A Wake-Up Call for Operational Efficiency Amid China's Oversupply
The global chemical industry is facing mounting challenges, with revenue declines and shrinking...
- 21-04-2025
Why Wrench Time Isn’t Improving: The Hidden Costs of Traditional Maintenance Scheduling
For years, industrial leaders have relied on a common but flawed assumption: "Better planning and...