Indian Disaster Shows Restarting Plants after a COVID-19 Lockdown Requires Connected Worker Solutions
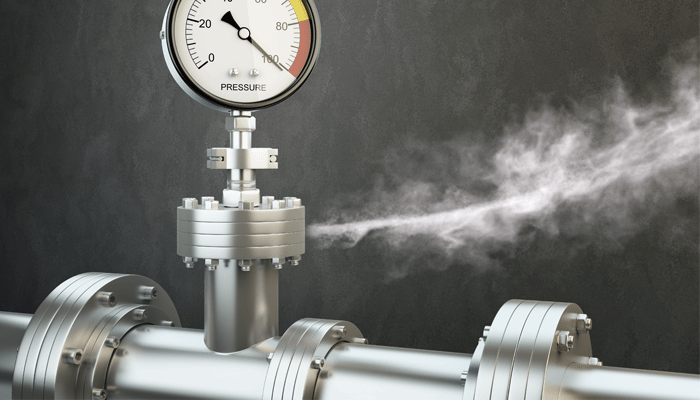
On May 7, 2020, India woke up to the news of poisonous gas leaking from a polymers plant in the southeastern city of Vizag. Toxic fumes leaking from a styrene storage tank killed 11 people and affected around 1,000 more living nearby. The company - LG Polymers - said that the tragedy happened while crews were restarting operations after a 40-day COVID-19 lockdown.
While the May 2020 leak is tiny in comparison, for Indians the incident brings back memories of the 1984 Bhopal disaster, the worst industrial accident in world history. There, more than 40 tons of deadly methyl isocyanate gas leaked at a Union Carbide plant in December 1984, killing 2,000 people and injuring over 200,000. Investigations later determined substandard operating and safety procedures were to blame for the tragedy. The cause of the recent May 7, 2020, Vizag accident, of course, awaits further study.
For executives, directors and managers in asset-intensive industries everywhere, the event is a wakeup call to reflect on their operations and maintenance management. Lockdown or no lockdown, some business operations can’t be deferred, even during a pandemic. Maintenance takes a top spot on the list. Inefficiencies in maintenance operations can result in grave consequences in terms of property damages or lost lives or both.
Vizag, India, is half a world away for Americans and Europeans. But that distance doesn’t diminish its importance and relevance for those in the chemical processing, oil & gas, mining, utilities and manufacturing industries that deal with hazardous substances on a daily basis. This event took place in India, but with today’s increasing global interconnectedness, the incident holds lessons and warnings for plants and industrial facilities in every corner of the world. Four of these are:
- Plants, production units, equipment and machinery need thorough and ongoing maintenance to sustain equipment reliability and ensure safe operations.
- Plants should put standard operating procedures in place to ensure occupational safety, particularly while resuming after any production stoppage or hiatus.
- Proper inventory levels of needed spare parts should be on-hand as a restart begins so that if a prompt repair is required, there is no delay that might turn a small issue into a serious problem.
- Maintenance personnel should be empowered with real-time information, and step by step, visual and guided work instructions to make tough decisions on the spot and they should be able to seamlessly share this information instantaneously up the decision-making tree.
What’s causing inefficiencies in plant maintenance?
We’re 20 years into the 21st century and more than 30 years into the Information Age. Yet, despite all the technical prowess available, a large number of industries and plants are still relying on paper-based forms to record data and transmit information. Maintenance managers need greater visibility into their maintenance operations, corrective repairs and equipment modification activities to ensure equipment reliability. For this to happen, maintenance managers should keep accurate, real-time, digital data on equipment health and work orders in their possession. Slow, cumbersome and error-prone paper-based processes simply can’t provide this.
Paper causes a lot of unnecessary travel between the back-office, maintenance shop and the field. And for every trip, a technician has to carry a binder of papers, manually collect data and input it into the ERP system. This causes considerable delays and far too often also results in errors, which can impact decision making at every level of the enterprise.
Connected Worker solutions can help avoid maintenance disasters like Vizag
Maintenance activities are collective efforts and need technicians and their managers to be on the same page to succeed. Empowering maintenance field forces and supervisors to quickly access real-time, critical information can improve operational efficiency, increase wrench time and productivity, reduce backlogs and reworks, and increase plant safety and compliance. Digital transformation offers a way to quickly and effectively achieve this.
Digital transformation leverages the full potential of agile, mobile PDAs like smartphones, wearables, and scanners, etc., to connect maintenance technicians, decision makers and the back-office system of record to deliver a connected worker experience to the front-line worker. Instead of collecting critical plant, unit and equipment data via paper, workers in the field can scan, photograph or video machinery and immediately relay vital information to their supervisors in real time. This eliminates costly delays caused by paper and of manual inputting of data into the ERP. Instead, key decision makers can learn immediately of a maintenance issue, make fact-based choices, issue work orders and follow progress as it happens using desktop apps.
While all the details of the Vizag tragedy have yet to be determined at this time, workers equipped with a Connected Worker solution could have uncovered evidence of a leak while conducting daily operator rounds using an electronic safety checklist. Because this checklist is mobile and digital, the results of the round would have been known in real time. Decision makers could have seen data that may have indicated a potential leak and been able to take appropriate action in time to prevent a disaster.
At Innovapptive, we’ve built a Connected Worker solution – mWorkOrder - that enables plant maintenance departments to do each of the activities described above and more. It transforms inefficient, reactive maintenance departments into flexible, agile preventative maintenance programs. Watch a video about mWorkOrder here.
To learn more about Connected Worker solutions and mWorkOrder, click here to schedule a free demo, or call us at 844-464- 6668. Our experts are standing by to introduce how digitally transforming your risk assessment can turn a business challenge into an advantage.
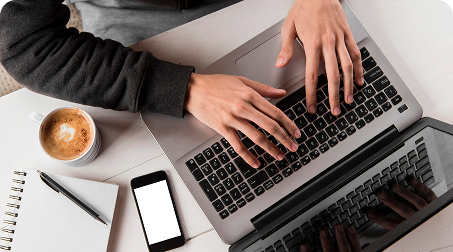
See It In Action
Schedule a personalized demo to see how our solutions can help your business thrive.
- 22-04-2025
The $3.6B Unlock: Solving the Chemical Industry’s Labor Crisis and EBITDA Pressure in One Move
“Constraints don’t slow innovation—they force it.”
- 21-04-2025
Chemical Industry's Margin Erosion: A Wake-Up Call for Operational Efficiency Amid China's Oversupply
The global chemical industry is facing mounting challenges, with revenue declines and shrinking...
- 21-04-2025
Why Wrench Time Isn’t Improving: The Hidden Costs of Traditional Maintenance Scheduling
For years, industrial leaders have relied on a common but flawed assumption: "Better planning and...