From Reactive to Proactive: Mastering Predictive Maintenance with a Connected Worker Solution in 2025
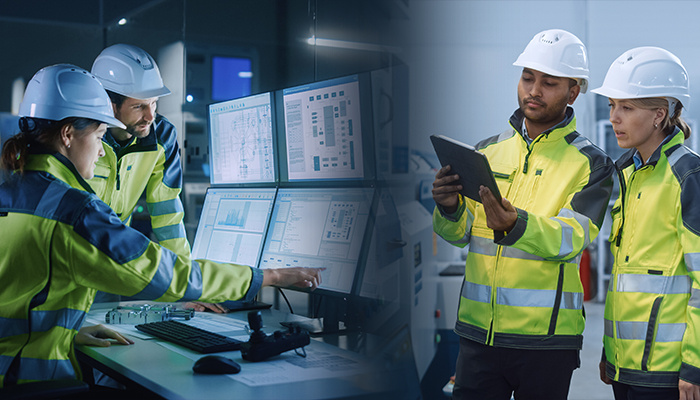
Key Takeaways
Significant Cost Savings: Implementing PdM can reduce maintenance costs by 25-30% compared to traditional methods (Deloitte, 2023). This proactive approach allows companies to optimize resources, lower emergency repair costs, and extend asset lifespan.
Enhanced Reliability and Compliance: PdM not only boosts equipment reliability by 70-75% but also ensures compliance with tightening environmental regulations, helping businesses avoid hefty fines (McKinsey & Company, 2023).
A Mobile Plant Maintenance App Can Help the Transition to PdM: An app streamlines data collection, real-time monitoring, and predictive analytics, facilitating the shift from reactive to predictive maintenance for optimized equipment reliability.
Introduction
Industrial plants are under increasing pressure to maintain smooth operations while meeting growing customer demands and profit margins. Reactive maintenance—fixing things after they break—is no longer sufficient. Predictive maintenance (PdM) is transforming industries, enabling businesses to foresee equipment failures before they happen, minimizing downtime, and maximizing efficiency. Mastering PdM is not just an option; it’s essential for staying competitive and seizing new opportunities. A connected worker solution can help industrial companies and plants transition to PdM. Read on to learn more.
The Limitations of Reactive Maintenance
Reactive maintenance—“fix it when it breaks”—is increasingly unsustainable as equipment demands grow. Here’s why:
- Unplanned Downtime: Reactive maintenance often leads to costly, unplanned downtime, with downtime costs averaging $260,000 per hour (Aberdeen Group). When critical equipment fails unexpectedly, production halts, leading to stress and costly recovery.
- Increased Maintenance Costs: Emergency repairs are typically more expensive than planned maintenance, with costs up to 50% higher compared to proactive approaches. Crisis mode often leads to escalating expenses.
- Reduced Asset Lifespan: Reactive maintenance shortens asset lifespan, increasing the risk of catastrophic failures. The U.S. Department of Energy notes that reactive maintenance can reduce equipment life by 30-40%, leading to more frequent breakdowns and costly replacements.
The Rise of Predictive Maintenance
Predictive maintenance offers a data-driven approach that goes beyond the “fix it when it breaks” mentality. By leveraging real-time monitoring and advanced analytics, PdM allows businesses to foresee potential equipment failures before they disrupt production.
Here’s how PdM is transforming maintenance:
- Real-Time Monitoring: Sensors and IoT devices continuously track equipment condition, providing insights into performance, wear and tear, and deviations from normal operations.
- Advanced Analytics: Machine learning algorithms analyze collected data, identifying patterns that may indicate impending failure, enabling action before a breakdown occurs.
- Core Technologies: PdM relies on technologies like IoT, big data analytics, and machine learning to connect equipment, process data, and improve predictive accuracy.
The Benefits of Predictive Maintenance
Predictive maintenance leverages data and analytics to transform industrial asset management, offering several key benefits:
- Increased Asset Reliability and Uptime: PdM enhances equipment reliability, reducing unplanned downtime by 70-75% and extending asset lifespan by 20-40% (Deloitte).
- Reduced Maintenance Costs: PdM can reduce maintenance expenses by 25-30%
compared to reactive or preventive strategies, optimizing parts inventory and labor requirements. - Improved Resource Allocation and Scheduling: PdM enables accurate prediction of maintenance needs, allowing for proactive scheduling during planned downtime, minimizing production impact.y
Enhanced Safety and Compliance: PdM ensures regulatory compliance through consistent, data-driven practices, reducing the risk of fines or shutdowns.
- Real-Time Monitoring: Sensors and IoT devices continuously track equipment condition, providing insights into performance, wear and tear, and deviations from normal operations.
Implementing Predictive Maintenance: A Step-by-Step Guide
Transitioning to predictive maintenance can seem daunting, but breaking it down into manageable steps makes the process smoother:
- Assess Current Strategy: Evaluate existing maintenance practices to identify where reactive maintenance causes issues like frequent downtime or high costs.
- Establish a Cross-Functional Team: Include maintenance managers, IT specialists, and operations personnel to oversee the PdM program, ensuring alignment with business goals.
- Implement IoT Sensors and Data Collection: Install IoT sensors on critical equipment to collect real-time performance data, forming the foundation of PdM efforts.
- Develop Predictive Models: Use machine learning and analytics to create models that analyze data, predict failures, and enable proactive action.
- Integrate with CMMS or EAM Systems: Seamlessly integrate PdM into existing systems to ensure efficient tracking and management of maintenance activities.
- Train Employees: Train staff on PdM processes and technologies, ensuring they understand how to interpret data and use predictive tools effectively.
Real-World Examples: Predictive Maintenance in Action
Here are examples of companies successfully using predictive maintenance:
Reducing Downtime: GE Aviation used PdM on jet engines to reduce downtime by 30% by predicting engine failures before they occurred.
Cutting Maintenance Costs: BP implemented PdM across its oil and gas operations, cutting maintenance costs by 20% and extending asset life.
Improving Scheduling: Siemens used PdM in wind turbine operations to optimize scheduling, reducing emergency maintenance activities by 50%.
Increasing Compliance: Duke Energy employed PdM to ensure compliance with environmental regulations, avoiding fines and ensuring adherence to standards.
Preparing for the Future with Predictive Maintenance
As we move toward 2025 and beyond, the maintenance landscape will continue to evolve, driven by industry trends and customer demands. Here’s why PdM is crucial for future-proofing your business:
- Customer Demands for Reliability: In today’s competitive market, downtime is costly. Customers expect near-perfect reliability, with downtime costing over $100,000 per hour (Gartner, 2022). PdM helps prevent failures and ensures smooth operation.
- Sustainability and Compliance: With tightening regulations, businesses must reduce their carbon footprint. PdM optimizes equipment performance, reducing energy consumption by up to 20% (McKinsey & Company, 2023).
Digital Transformation: PdM is at the forefront of digital transformation, helping businesses harness real-time data for better decision-making, reducing maintenance costs by 30%, and decreasing downtime by 70% (Deloitte, 2023).
To Sum It Up
Predictive maintenance isn’t just a trend—it’s the future of industrial operations. By proactively monitoring and maintaining equipment, businesses can reduce unexpected downtime, lower costs, and extend asset life. Embrace PdM to stay competitive and thrive in the future. And, when transitioning to PdM, consider implementing a connected worker solution and a mobile plant maintenance app to achieve further success.
Move to Predictive Maintenance with Innovapptive’s Connected Worker Solution
In today’s industrial landscape, transitioning from reactive to predictive maintenance is crucial for staying competitive. Innovapptive’s Connected Worker Platform, including its SAP Mobile Work Order Management app (mWorkOrder), offers the tools needed for a smooth and effective transition.
- Enhanced Mobile Access: The platform provides an intuitive, interactive user interface to create and update work orders with real-time data, allowing maintenance teams to respond quickly to issues and minimize downtime.
- Streamlined Workflows: Automate the entire maintenance process, reducing administrative burdens and ensuring tasks are completed efficiently, boosting productivity.
- Computer Vision: Advanced computer vision enables inspectors to spot and report issues early, increasing the time between failures, and ensuring safe, productive operations.
- Anomaly Detectors: Instantly create a mobile corrective work order whenever an operator or technician inputs a rating outside a pre-defined range during a round or inspection.
- Asset 360 Dashboard: Get a quick, comprehensive snapshot of an asset’s history, past work details, and current conditions, while keeping tabs on expenses and issues — all in one place, with smart suggestions.
- Comprehensive Reporting and Compliance: Effortlessly generate compliance reports, ensuring all activities meet industry regulations and help avoid costly fines and audits.
Partnering with Innovapptive enhances maintenance efficiency and reliability, positioning your plant to thrive in a competitive environment.
FAQ: Predictive Maintenance for Industrial Plants
What is predictive maintenance?
PdM uses real-time data and analytics to predict equipment failures, allowing preemptive action and reducing downtime.
How can predictive maintenance reduce costs?
PdM can lower maintenance expenses by 25-30%, optimizing resources and extending equipment lifespan (Deloitte).
What role does technology play in PdM?
PdM relies on IoT, big data analytics, and machine learning for real-time monitoring and accurate failure predictions.
How does PdM improve reliability and compliance?
PdM enhances reliability by reducing unplanned downtime by up to 75% and ensures compliance by identifying risks early.
Is transitioning to PdM difficult?
While initial investments in technology and training are needed, Innovapptive’s Connected Worker Solution simplifies the transition.
How can Innovapptive help me transition to predictive maintenance?
Innovapptive’s Connected Worker Solution—including the mobile work order management app, mWorkOrder—integrates IoT sensors and advanced analytics with SAP systems, enabling smooth transitions to predictive maintenance through proactive scheduling, mobile access, streamlined workflows, and comprehensive reporting for improved operational efficiency.
What are the key benefits of using the mWorkOrder mobile work order management app?
mWorkOrder offers up to a 20% increase in wrench time, 50% reduction in work backlog, 80% decrease in preventable failures, and 26% lower maintenance costs.
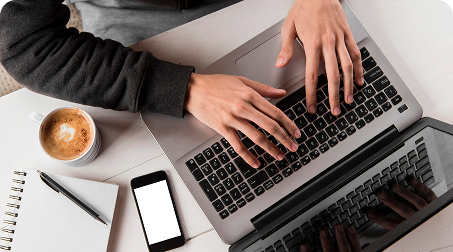
See It In Action
Schedule a personalized demo to see how our solutions can help your business thrive.
- 20-08-2025
Building the future of Industrial Operations with Innovapptive and AWS
Most manufacturers have already gone digital. Yet business outcomes haven’t moved in step. Many...
- 22-04-2025
The $3.6B Unlock: Solving the Chemical Industry’s Labor Crisis and EBITDA Pressure in One Move
“Constraints don’t slow innovation—they force it.”
- 21-04-2025
Chemical Industry's Margin Erosion: A Wake-Up Call for Operational Efficiency Amid China's Oversupply
The global chemical industry is facing mounting challenges, with revenue declines and shrinking...