Meet Agentic AI: The Preventive Maintenance Superhero You Didn’t Know You Needed
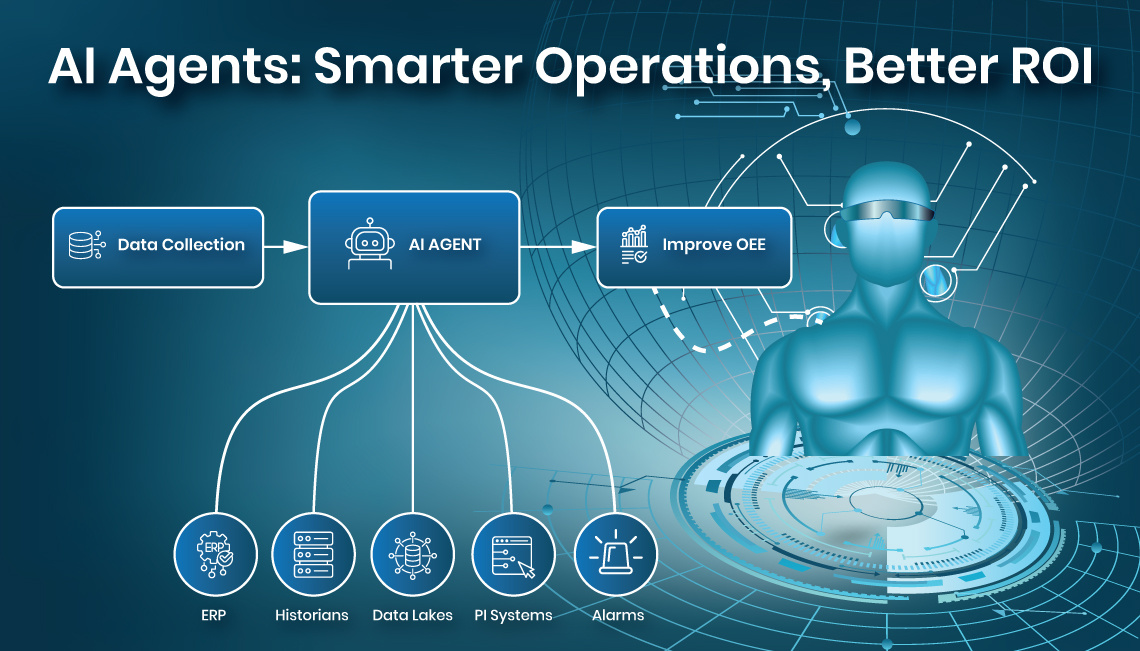
Every maintenance manager faces the same dilemma—how much maintenance is too much, and how little is too risky? Get it wrong, and you’re either burning cash on unnecessary servicing or dealing with costly unplanned downtime. The industry benchmark for Maintenance Cost as a percentage of Replacement Asset Value (RAV) tells the story: world-class operations stay below 3%, while inefficient ones creep past 5-7%, bleeding money on both ends.
Enter Agentic AI — your new digital maintenance superhero. Think of it as Iron Man’s J.A.R.V.I.S. for industrial maintenance—an intelligent system that doesn’t just detect problems but thinks, plans, and acts in real time. Unlike traditional maintenance tools that only provide insights, Agentic AI takes action, optimizing preventive maintenance schedules, automating task execution, and ensuring that every dollar spent on maintenance delivers maximum value.
Why Industries Need a Hero Like Agentic AI—Now More Than Ever
In the dynamic landscape of process manufacturing industries, maintaining operational efficiency is paramount. Traditional maintenance strategies, often reliant on time-based preventive maintenance, may not suffice in today’s fast-paced environment. The difference between being under-maintained (where failures are frequent) and over-maintained (where costs spiral out of control) is razor-thin. Agentic AI finds the perfect balance—optimizing maintenance decisions in real time to keep costs low and asset availability high.
Introducing Agentic AI in Preventive Maintenance
Agentic AI refers to autonomous systems that integrate machine learning, real-time analytics, and decision-making capabilities to optimize maintenance processes. By analyzing vast datasets from IoT sensors and industrial maintenance software, these intelligent agents can predict equipment failures, schedule maintenance tasks, and execute them autonomously. This shift from traditional time-based preventive maintenance to AI-driven strategies enhances operational efficiency and reduces unplanned downtime.
Key Features of Agentic AI in Maintenance
- Predictive Analytics: AI-powered models analyze historical and real-time data to anticipate equipment failures, preventing costly breakdowns.
- Automated & Adaptive Scheduling: Dynamically adjusts maintenance plans based on real-time equipment health, operational priorities, and predictive insights.
- Autonomous Task Execution: AI-driven systems handle routine maintenance tasks, inspections, and diagnostics, reducing manual intervention.
- Conversational AI for Frontline Workers: Natural language processing (NLP) enables intuitive, hands-free interactions for faster issue resolution and decision-making.
- AI-Enhanced Inspections: Computer vision technology automates visual inspections, identifying defects and anomalies with greater accuracy.
- Continuous Learning & Optimization: Advanced machine learning models refine recommendations over time, adapting to new patterns and evolving operational needs.
Oil & Gas operations rely on complex machinery and infrastructure that operate in extreme conditions. Unexpected failures can lead to costly downtime, safety risks, and environmental hazards. AI-driven preventive maintenance helps predict failures before they occur, ensuring operational efficiency and reliability.
- Data Collection: AI gathers sensor data from drilling rigs, pipelines, compressors, and offshore platforms, along with historical maintenance logs.
- AI Detection: AI analyzes vibration patterns, temperature fluctuations, pressure levels, and corrosion rates to detect early signs of equipment failure.
- Decision-Making: AI assesses the severity of detected anomalies and determines if immediate maintenance is required.
- Automated Execution: If high priority, AI automatically generates work orders, assigns technicians, and recommends spare parts for proactive replacement.
- Maintenance Execution: Technicians carry out inspections, repairs, or part replacements based on AI-driven recommendations.
- Feedback & Optimization: AI refines maintenance schedules based on equipment performance, failure patterns, and real-time operational data.
- Continuous Improvement: The system continuously learns from past maintenance actions, improving failure predictions and optimizing maintenance efficiency.
By leveraging AI for preventive maintenance, Oil & Gas companies can enhance equipment reliability, minimize unplanned downtime, and improve worker safety while reducing operational costs.
Enhancing Operational Efficiency through AI-Driven Preventive Maintenance
Implementing Agentic AI in preventive maintenance offers numerous benefits that directly impact operational efficiency and workforce productivity.
1. Real-time Data and Reduced Downtime
By analyzing real-time data from equipment sensors, Agentic AI can identify patterns indicative of potential failures. This predictive capability allows maintenance teams to address issues before they escalate, significantly reducing unplanned downtime. For instance, AI-driven systems can predict equipment failures 72 hours in advance with 95% accuracy, enabling proactive interventions.
2. Optimized Preventive Maintenance Scheduling
Traditional preventive maintenance schedules often lead to unnecessary servicing of equipment. Agentic AI optimizes these schedules by assessing the actual condition of assets, ensuring maintenance activities are performed only when necessary. This approach not only extends equipment lifespan but also reduces maintenance costs.
3. Autonomous Maintenance Execution
Agentic AI systems are capable of executing routine maintenance tasks autonomously. By automating these processes, companies can free up their workforce to focus on more complex tasks, thereby enhancing overall productivity. For example, AI-driven mobile maintenance management keeps teams connected with real-time alerts and repair insights, streamlining operations.
4. Integration with Enterprise Asset Management Systems
Integrating Agentic AI with existing enterprise asset management (EAM) systems provides a holistic view of asset health and maintenance activities. This seamless integration ensures that all maintenance decisions are data-driven and aligned with the organization’s operational goals. AI-driven preventive maintenance solutions can automate the entire workflow, ensuring the right work gets done at the right time without wasted effort.
Innovapptive’s Role in AI-Driven Preventive Maintenance
Innovapptive offers cutting-edge solutions to transform preventive maintenance practices in process manufacturing industries. Our connected worker platform empowers organizations to:
How Innovapptive Leverages AI Agents to Automate Maintenance—From Detection to Execution
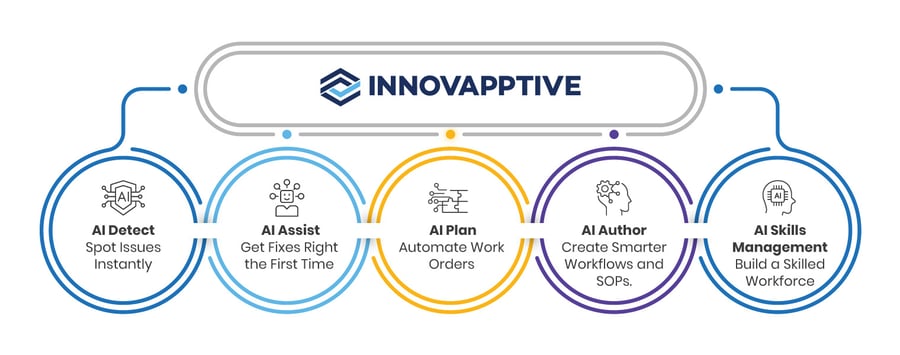
- AI Detect - Spot Problems To Minimize Downtime: Instead of relying on manual inspections, AI Detect identifies and alerts teams to potential risks, enabling proactive intervention to minimize downtime. It analyzes equipment conditions in real time, instantly detecting issues so the necessary action can be taken—eliminating unexpected breakdowns and last-minute scrambling.
- AI Assist - Get Fixes Right the First Time: When an issue is detected, maintenance teams no longer need to waste time searching for solutions. AI Assist suggests the best course of action—whether it’s adjusting machine settings, replacing a part, or scheduling lubrication. With step-by-step guidance, technicians can resolve issues faster and with fewer mistakes, improving first-time fix rates and MTTR.
- AI Plan - Automate Work Order Planning: Once an issue is detected and assessed, AI Plan expedites the process of creating work orders in a few clicks. It considers asset criticality and technician availability to optimize preventive maintenance. No more guesswork, just smart scheduling that prevents downtime and maximizes productivity.
- AI Author - Create Smarter Workflows and SOPs: Instead of filling out forms manually or hunting for the right SOP, AI Author automates workflow creation. It helps supervisors and managers generate digital work orders, checklists, and SOPs with pre-filled data and best practices so technicians can execute tasks quickly and correctly.
- AI Skills Management & RCA Insights: Empower technicians with AI-driven RCA, toolbox talks, and supervisor feedback to enhance problem-solving, retain knowledge, and refine troubleshooting—building a skilled workforce that minimizes failures and downtime.
By automating the entire preventive maintenance cycle, AI ensures less downtime, fewer manual errors, and a more efficient maintenance team.
Future Agentic AI Trends in Manufacturing
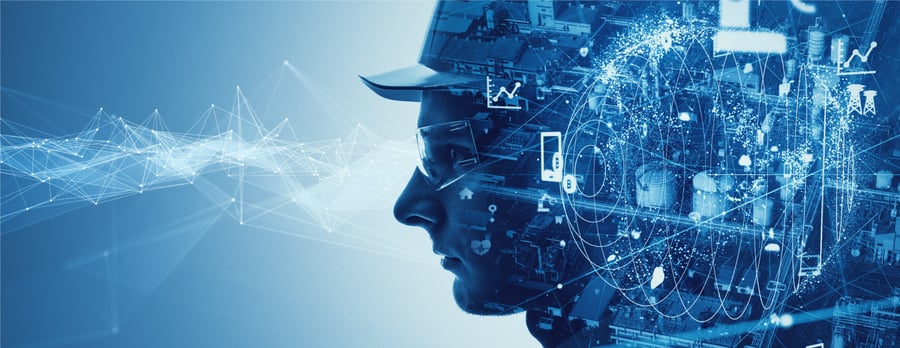
- Self-Learning & Autonomous Decision-Making: Agentic AI will evolve beyond rule-based automation, using reinforcement learning and adaptive AI to make real-time decisions without human intervention.
- AI-Driven Predictive & Preventive Maintenance: AI will shift from just predicting failures to prescribing optimal maintenance actions, adjusting schedules dynamically to prevent downtime and maximize asset longevity.
- Human-AI Collaboration & Connected Worker Solutions: AI Agents will act as co-pilots for frontline workers, offering real-time insights, guiding repairs, and even autonomously handling routine maintenance tasks.
- AI-Enabled Operations, Maintenance & Inventory Synchronization: Agentic AI will connect operations, maintenance, and inventory management, ensuring seamless maintenance scheduling, spare parts availability, and real-time stock optimization to prevent production disruptions.
- Multi-Agent AI Ecosystem for Industrial Connectivity: Future AI systems will integrate with SCADA, Enterprise Asset Management (EAM) platforms like SAP, IBM Maximo, IoT networks, and ERP systems to enable intelligent automation, cross-functional data sharing, and optimized process execution across the enterprise.
Unlock the Future of Maintenance with Agentic AI
In today’s fast-evolving industrial landscape, Agentic AI is the game-changer maintenance teams have been waiting for. By shifting from static schedules to intelligent, automated maintenance, organizations can reduce maintenance costs as a % of RAV, increase asset uptime, and boost operational efficiency. Businesses that adopt these methods in controlling their production processes will be able to experience new forms of growth, new forms of innovation, and new forms of success in a rapidly evolving environment.
They can use Agentic AI as an opportunity to build a stronger, adaptive, and effective process manufacturing environment.
Ready to see Agentic AI in action? Request a Demo Today
FAQ Section
1. What is Agentic AI in maintenance?
Agentic AI in maintenance refers to autonomous AI systems that can analyze equipment data, detect early warning signs of failure, and make intelligent decisions without human intervention. These AI agents not only recommend maintenance actions but can also automate work order creation, assign tasks to technicians, and optimize maintenance schedules dynamically.
2. How does AI reduce unplanned downtime?
Innovapptive’s AI-powered preventive maintenance solutions proactively reduce unplanned downtime by leveraging real-time asset monitoring, predictive analytics, and AI-driven decision-making. With AI-powered anomaly detection, maintenance teams receive early alerts about potential failures before they escalate.
Key capabilities include:
- AI-Driven Work Order Automation: Automatically generates and assigns work orders.
- Intelligent Scheduling & Resource Optimization: Balances workloads and ensures the right technicians, tools, and spare parts are available.
- Mobile Maintenance Execution: Empowers frontline workers with AI-guided workflows, reducing delays in issue resolution.
- Connected Worker Insights: Integrates with SCADA, EAM, and IoT systems to provide a 360-degree view of asset health, enabling smarter decision-making.
3. What industries benefit from AI-driven preventive maintenance?
AI-driven preventive maintenance is transforming asset-intensive industries, including:
- Oil & Gas: Predicts pipeline corrosion, compressor failures, and rotating equipment inefficiencies to prevent costly shutdowns.
- Manufacturing: Optimizes production uptime by monitoring CNC machines, conveyor belts, and robotics for early failure signs.
- Chemical Processing: Ensures regulatory compliance by detecting catalyst degradation, valve leaks, and reactor inefficiencies in real time.
- Mining & Metals: Reduces unexpected failures in heavy-duty machinery, crushers, and conveyor systems while improving safety.
- Energy & Utilities: Enhances grid reliability and prevents transformer overheating, turbine failures, and power outages through AI-driven asset monitoring.
FAQ Section
1. What is Agentic AI in maintenance?
Agentic AI in maintenance refers to autonomous AI systems that can analyze equipment data, detect early warning signs of failure, and make intelligent decisions without human intervention. These AI agents not only recommend maintenance actions but can also automate work order creation, assign tasks to technicians, and optimize maintenance schedules dynamically.
2. How does AI reduce unplanned downtime?
Innovapptive’s AI-powered preventive maintenance solutions proactively reduce unplanned downtime by leveraging real-time asset monitoring, predictive analytics, and AI-driven decision-making. With AI-powered anomaly detection, maintenance teams receive early alerts about potential failures before they escalate.
Key capabilities include:
- AI-Driven Work Order Automation: Automatically generates and assigns work orders.
- Intelligent Scheduling & Resource Optimization: Balances workloads and ensures the right technicians, tools, and spare parts are available.
- Mobile Maintenance Execution: Empowers frontline workers with AI-guided workflows, reducing delays in issue resolution.
- Connected Worker Insights: Integrates with SCADA, EAM, and IoT systems to provide a 360-degree view of asset health, enabling smarter decision-making.
3. What industries benefit from AI-driven preventive maintenance?
AI-driven preventive maintenance is transforming asset-intensive industries, including:
- Oil & Gas: Predicts pipeline corrosion, compressor failures, and rotating equipment inefficiencies to prevent costly shutdowns.
- Manufacturing: Optimizes production uptime by monitoring CNC machines, conveyor belts, and robotics for early failure signs.
- Chemical Processing: Ensures regulatory compliance by detecting catalyst degradation, valve leaks, and reactor inefficiencies in real time.
- Mining & Metals: Reduces unexpected failures in heavy-duty machinery, crushers, and conveyor systems while improving safety.
- Energy & Utilities: Enhances grid reliability and prevents transformer overheating, turbine failures, and power outages through AI-driven asset monitoring.
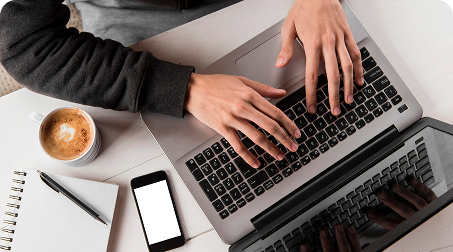
See It In Action
Schedule a personalized demo to see how our solutions can help your business thrive.
- 20-08-2025
Building the future of Industrial Operations with Innovapptive and AWS
Most manufacturers have already gone digital. Yet business outcomes haven’t moved in step. Many...
- 22-04-2025
The $3.6B Unlock: Solving the Chemical Industry’s Labor Crisis and EBITDA Pressure in One Move
“Constraints don’t slow innovation—they force it.”
- 21-04-2025
Chemical Industry's Margin Erosion: A Wake-Up Call for Operational Efficiency Amid China's Oversupply
The global chemical industry is facing mounting challenges, with revenue declines and shrinking...