How AI is Transforming Manufacturing with Automation & Predictive Insights
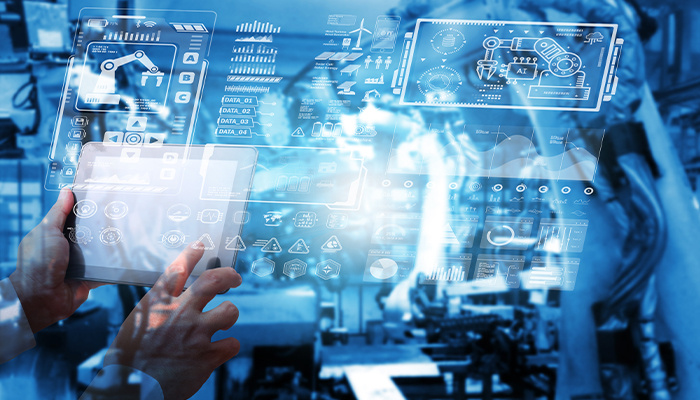
Rising Costs, Downtime, and Inefficiencies: How AI Is Reshaping Manufacturing
The manufacturing industry is evolving rapidly, driven by the need for greater efficiency, lower costs, and higher quality standards. Traditional methods like manual inspections and scheduled maintenance have served well for decades—but they often fall short in today’s fast-paced, complex environments. Unplanned downtime, for instance, remains a major challenge, costing U.S. manufacturers an estimated $50 billion annually, according to Siemens.
This is where Artificial Intelligence is beginning to make a real difference. Rather than reacting to problems after they occur, AI enables manufacturers to anticipate issues, make faster decisions, and keep operations running smoothly. AI-powered predictive maintenance is already showing results, with Siemens reporting up to a 50% reduction in unplanned downtime and a 40% cut in maintenance costs. And the long-term gains go beyond maintenance. IDC projects that AI and other operational technologies could boost global manufacturing productivity by 5% by 2025, signaling a major shift in how the industry operates.
Smarter Manufacturing: AI’s Role in Automation and Efficiency
Unlike traditional automation, which follows fixed workflows, AI-powered manufacturing systems learn, adapt, and improve over time. Machine learning models analyze production data, identify inefficiencies, and make real-time adjustments to enhance operational performance.
By integrating AI into manufacturing, companies are moving from reactive decision-making to proactive optimization. Production lines can now detect bottlenecks before they cause delays, and machines can self-adjust to maintain peak efficiency.
AI also plays a crucial role in predictive analytics, helping manufacturers anticipate issues rather than react to them. This results in a more agile and cost-effective manufacturing ecosystem, where resources are allocated intelligently and productivity remains high.
Predictive Maintenance: Eliminating Downtime Before It Happens
Imagine a critical machine on a production line suddenly breaking down in the middle of a high-volume order—halting operations, delaying shipments, and driving up costs. This is a common scenario manufacturers face with traditional maintenance strategies, which often rely on reactive repairs or scheduled servicing that doesn’t reflect the actual condition of equipment.
AI-powered predictive maintenance eliminates this inefficiency. By continuously monitoring equipment through IoT sensors and advanced analytics, AI detects subtle performance deviations that signal potential failures. These insights allow manufacturers to schedule maintenance only when needed, preventing costly breakdowns while optimizing asset lifespan.
The impact is significant. Reduced unplanned downtime, lower maintenance costs, and increased productivity make AI-driven predictive maintenance a game-changer for manufacturers aiming to maximize efficiency.
AI-Driven Quality Control: Precision Without Human Error
Ensuring product quality is critical in manufacturing, but traditional inspection methods rely heavily on manual processes that are slow, inconsistent, and prone to human error. AI is transforming quality control by introducing automated inspection systems powered by computer vision and deep learning.
AI-powered quality control systems use high-speed cameras to scan products in real time, identifying defects with unmatched accuracy. These systems detect microscopic flaws that human inspectors might miss, ensuring that only high-quality products reach customers.
By integrating AI-driven quality control, manufacturers reduce waste, minimize rework costs, and enhance brand reputation. The result is a streamlined production process that maintains high precision and consistency at scale.
Enhancing Worker Safety with AI-Powered Monitoring
Manufacturing environments come with inherent risks, from machine-related injuries to hazardous material exposure. AI is enhancing worker safety by providing real-time monitoring and automated risk detection.
AI-powered computer vision systems analyze video feeds to detect unsafe behaviors, such as missing protective gear or improper equipment handling. Instant alerts notify supervisors, allowing for immediate intervention before accidents occur.
Additionally, AI-driven wearables track worker fatigue and stress levels, preventing accidents caused by exhaustion. Automated compliance monitoring further reduces the risk of human error in safety procedures, ensuring regulatory adherence.
With AI, manufacturers create safer work environments, reducing injuries and improving workforce well-being.
How Innovapptive is Leading AI-Powered Digital Transformation
Despite the benefits of AI, many manufacturers struggle with manual processes, disconnected teams, and inefficient workflows. Innovapptive’s AI-powered Connected Worker Platform bridges this gap by integrating real-time data access, intelligent automation, and predictive analytics.
AI-Driven Asset Management & Predictive Maintenance
Innovapptive’s AI-powered maintenance solutions eliminate inefficiencies by digitizing work orders, providing real-time asset tracking, and using predictive analytics to optimize servicing schedules. This ensures seamless equipment performance and reduced downtime.
Workforce Collaboration & Digital Work Instructions
Frontline workers often rely on outdated, paper-based instructions. Innovapptive’s digital work instructions enable mobile access to SOPs, real-time task assignments, and instant issue resolution, boosting workforce efficiency.
AI-Powered Inventory & Safety Management
With mobile-enabled kitting and staging, work orders are automatically linked to the required parts, ensuring kits are prepared in advance and ready just in time. Technicians no longer wait for materials to be assembled, reducing idle time at the job site. This streamlined process minimizes delays, improves task execution, and significantly enhances Mean Time to Repair (MTTR). Additionally, Innovapptive’s AI-powered safety solutions can automate compliance monitoring through digital daily huddles, toolbox talks, and AI-driven permit management. This proactive approach ensures safety protocols are consistently followed, reducing risk and enhancing overall workplace security.
By leveraging AI across maintenance, workforce collaboration, and inventory management, Innovapptive empowers manufacturers to improve efficiency, reduce downtime, and enhance operational safety.
Conclusion: The Future of AI in Manufacturing
AI is no longer a futuristic concept—it is actively transforming manufacturing today. Companies that embrace AI-powered solutions are seeing higher efficiency, improved quality control, optimized supply chains, and safer work environments.
With Innovapptive’s AI-powered Connected Worker Platform, manufacturers can stay ahead of industry challenges, reduce costs, enhance workforce productivity, and drive continuous improvement.
Are you ready to leverage AI for smarter manufacturing? Discover how Innovapptive’s AI-driven solutions can help your business stay competitive in the digital era.
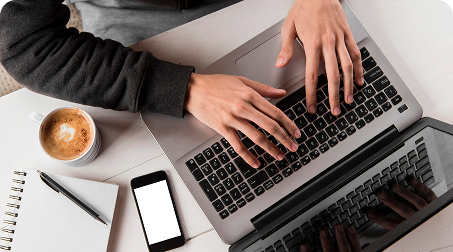
See It In Action
Schedule a personalized demo to see how our solutions can help your business thrive.
- 20-08-2025
Building the future of Industrial Operations with Innovapptive and AWS
Most manufacturers have already gone digital. Yet business outcomes haven’t moved in step. Many...
- 22-04-2025
The $3.6B Unlock: Solving the Chemical Industry’s Labor Crisis and EBITDA Pressure in One Move
“Constraints don’t slow innovation—they force it.”
- 21-04-2025
Chemical Industry's Margin Erosion: A Wake-Up Call for Operational Efficiency Amid China's Oversupply
The global chemical industry is facing mounting challenges, with revenue declines and shrinking...