SAP PM Solution: Optimize Maintenance, Improves Wrench Time
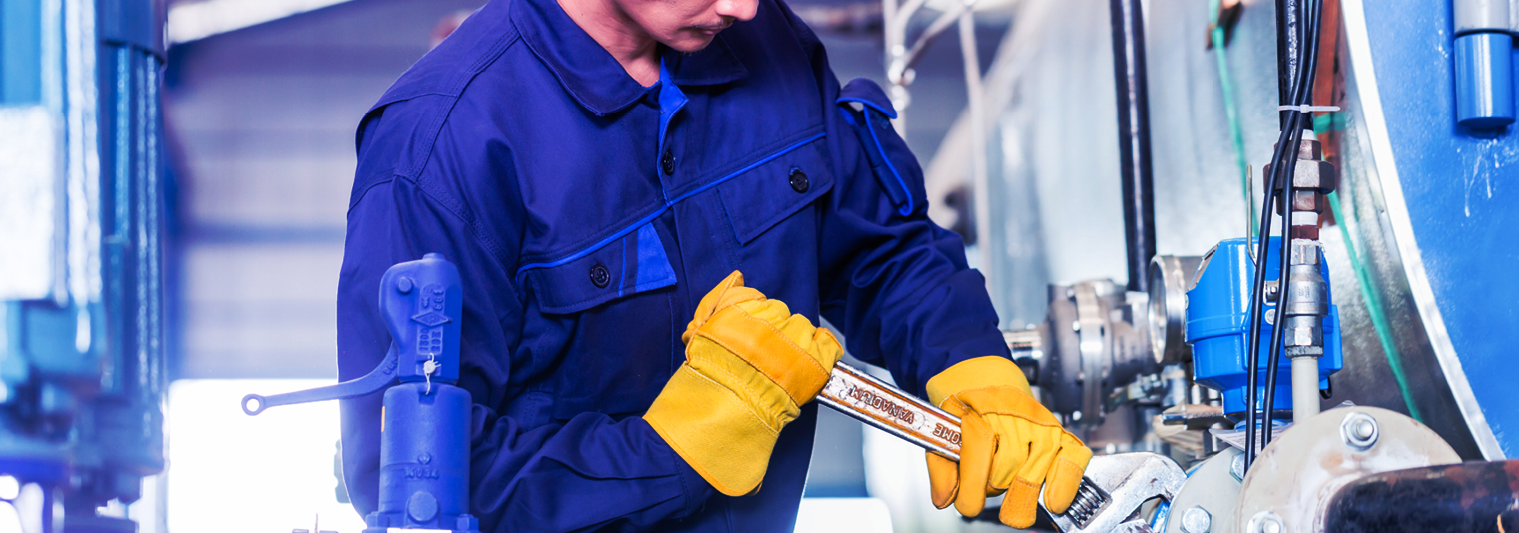
Efficient Plant Magazine illustrates the significant financial impact of maintenance workforce efficiency. A highly efficient operation with 74% wrench time spends $100 million/yr. on maintenance labor. A highly inefficient maintenance operation would spend more than four times that amount (or more than $400 million annually) to complete the same volume of work. What is the translation? The inefficient maintenance operation would waste $300 million a year due to inefficiency.
Fortunately, for companies wanting to reverse those low numbers, a solution exists through a Connected Worker Strategy that makes a Mobile Plant Maintenance and work instruction application front and center of their strategy.
What Negatively Impacts a Maintenance Technician’s Wrench Time?
Why is it the average maintenance front-line worker only spends 120 to 150 minutes a day turning a tool? It's several things, including:
- Waiting on instructions,
- Not having the right parts/equipment at the right time,
- Ineffective route planning for work orders and jobs,
- Repeated travel back and forth from the worksite to the office/storeroom to collect parts, manuals and get assistance,
- No access to an asset’s maintenance history, equipment drawings, and details or service manuals.
Essentially, then, time is wasted on preparing, transitioning, and/or waiting for materials, equipment or information.
To improve actual wrench time, an organization needs to identify and eliminate barriers preventing maintenance technicians from doing their jobs efficiently. One of the most effective ways to improve your technicians' wrench time is to streamline your organization's planning and scheduling with a mobile work order and work instruction application to improve your preventive/proactive maintenance procedures. Effective planning/scheduling and closing the last mile gap of executing the job with a mobile plant maintenance and work instruction application will help ensure that plant maintenance work is well planned, aiding in work orders being completed according to priorities.
To be more productive, a maintenance team needs to have the following available before starting any work order:
- Key asset operational specifications,
- Full equipment maintenance history,
- The right parts/tools,
- Guiding instructions.
Having these readily available as the technician heads out for the job:
- Improves a maintenance workforce’s productivity,
- Reduces delays during jobs,
- Boosts the bottom line.
Mobile Plant Maintenance: A Connected Worker Strategy for Improved Wrench Time and Operational Efficiencies
A maintenance team is typically mobile; it’s going in all directions throughout the plant. Therefore, to increase their productivity and raise their wrench time, it makes sense to provide a solution to keep them as mobile, agile and flexible as possible. Enter the Connected Worker strategy.
What is a Connected Worker strategy? It’s the next step in digital transformation. It’s the joining of technology and digital trends such as Cloud, mobile, wearables (smart glasses and smartwatches), augmented reality, AI/ML, virtual assistants and other connected products to change a front-line worker’s life for the better. The ultimate goal of a Connected Worker solution or platform is to help the front-line worker get his or her job done faster, better, cheaper and safer.
Mobile Plant Maintenance is the extension of the Connected Worker strategy to maintenance. Rather than using slow, cumbersome and error-prone manual data collection processes to gather, share and disseminate operational information, front-line workers instead use mobile devices to digitally perform tasks. What activities are covered in Mobile Plant Maintenance?
- Integration with SAP or IBM Maximo
- Work orders,
- Risk assessments,
- Inspections,
- Checklists,
- Notifications,
- Instructions,
- Check inventory/materials,
- View videos, pdfs and photos,
- Annotate and attach pdfs and photos,
- View objects,
- Time capture.
With these Connected Worker capabilities, front-line maintenance technicians can be more productive in their day. They can spend less time preparing, transitioning, and/or waiting for materials, equipment or information, and more time turning the wrench and accomplishing measurable work.
Want to Learn More?
Innovapptive offers the only Connected Worker platform that digitizes the last mile of your front-line workers into SAP and IBM. We’d like to show you how Mobile Plant Maintenance successfully start and complete your journey to more efficient, safe and productive plant maintenance (watch a short video here). Schedule a free demo today by calling 844-464-6668 or by clicking here.
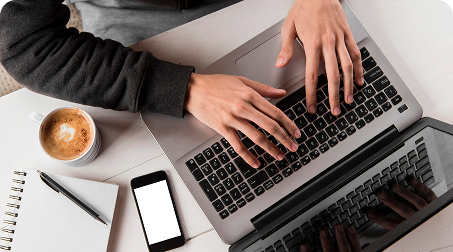
See It In Action
Schedule a personalized demo to see how our solutions can help your business thrive.
- 20-08-2025
Building the future of Industrial Operations with Innovapptive and AWS
Most manufacturers have already gone digital. Yet business outcomes haven’t moved in step. Many...
- 22-04-2025
The $3.6B Unlock: Solving the Chemical Industry’s Labor Crisis and EBITDA Pressure in One Move
“Constraints don’t slow innovation—they force it.”
- 21-04-2025
Chemical Industry's Margin Erosion: A Wake-Up Call for Operational Efficiency Amid China's Oversupply
The global chemical industry is facing mounting challenges, with revenue declines and shrinking...