Mobility in Manufacturing: Enhancing Productivity and Eliminating Bottlenecks
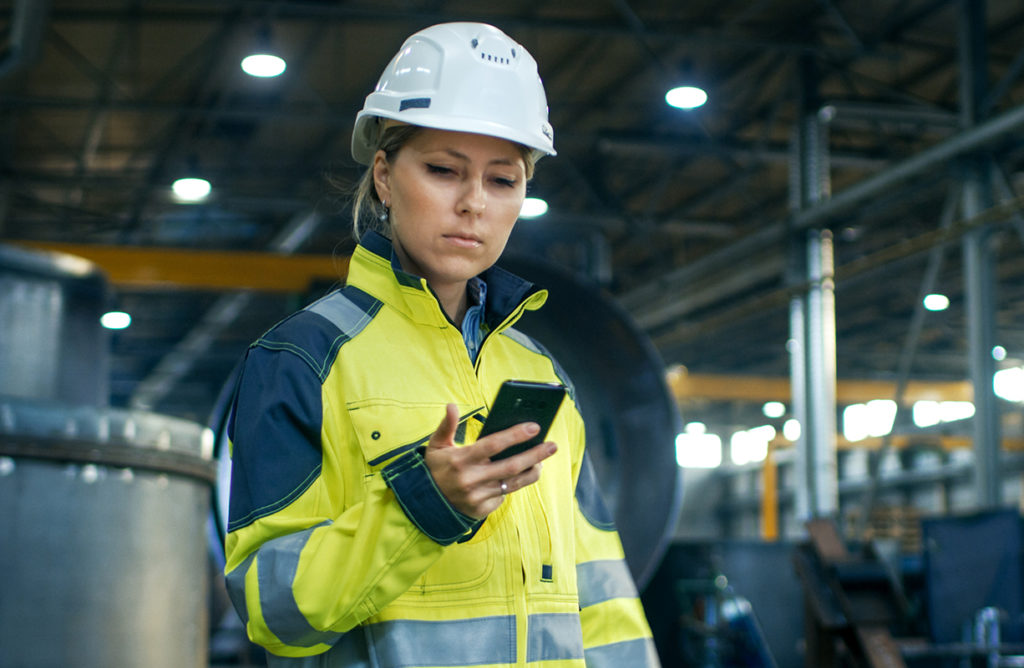
The manufacturing industry is under pressure to increase their output, maximize employees’ productivity, and profitability. Manufacturing companies of all sizes, regardless of their business line, are looking to newer markets to boost future growth. Zero-defect manufacturing is essential to be cost-effective.
Majority of manufacturing companies have plants and offices at different locations and are equipped with a variety of large machines and heavy assets. To keep such machinery consistently running effectively companies rely on leading enterprise planning software such as SAP ERP yet, many times, their employees still use paper-based manual processes to transfer information. Such tedious, error-prone manual processes further impact production activities down the line which, adversely impacts the business. Errors such as incorrect bills, inventory reports, etc negatively impact production and much more. Corrections to these errors leads to rework and waste of employees’ time and effort.
A leading concern for many CIOs is the overhaul and improvement across all business functions, from the procurement of raw material to finished goods to reaching out to customers, thus improving time to market. Enabling greater production and service agility with existing IT systems/resources is must to achieve success for any manufacturing company. Companies need the best solution to drive higher revenue growth by utilizing the available IT infrastructure they have in place.
Increasing employees’ productivity as it directly contributes to growth and is vital for company survival in this competitive market is another chief concern for any manufacturing company. Providing employees access to necessary information whenever, and wherever, they need to perform well is one of the top secrets to increasing productivity in manufacturing. Integrating the right mobile solution to enhance their workforce productivity can achieve all of this in one fell swoop.
In a nutshell, it is crucial for manufacturing companies to stay up to date with the present market scenario and be a step ahead of the competition to increase the profitability. They can increase uptime, react faster to issues, and satisfy customers more consistently when they have greater visibility into their operations and asset performance. Real-time information and instant updates are critical to the production process to eliminate revenue loss. The more accurate and consistent the data is, the better the decision-making process.
"CIOs working at manufacturing companies now rank the investment in mobile technologies as a top priority". (Gartner)
Mobility in manufacturing is one such recent adoption enabling manufacturers around the globe to match their capability enhancements and resource mobilization with critical improvement in business processes. Mobility solutions are transforming the manufacturing industry by simplifying business processes and making employees’ jobs easier. While enhancing employee productivity and simultaneously reducing cost, mobile-based solutions ensure higher accuracy by converting time-consuming manual processes into automated ones. Mobile solutions reduce the data gap and significantly increase responsiveness to changing market conditions and customer requirements.
Improving Workforce Productivity with Instant Mobilization
Innovapptive’s mServiceOrder is the premier mobile solution for Field Service Management. Equipped with all the field-ready functionality needed to improve efficiency in the field from any device (mobile), mServiceOrder, an SAP® Certified Mobile solution, helps improve workforce productivity while optimizing field service operations. It allows service crews to create service orders and notifications, and view Bill of Materials with ease while reducing service times.
Designed from the ground up with field technicians and engineers in mind, mServiceOrder provides a refined interface, consistent access, and targeted service workflows regardless of internet connectivity, reducing service costs and boosting service levels while avoiding unnecessary trips with guided route optimization. The mobile solution puts visibility in your techs’ hands and enables viewing of planned service orders on specific dates to help prepare and complete service calls without skipping a beat.
Innovapptive’s mInventory, an SAP® certified solution, enables users to perform day-to-day inventory transactions through handheld devices and laptops by accessing the master data of SAP. Leveraging SAP Inventory Management (IM), Warehouse Management (WM) and Extended Warehouse Management (EWM) modules, mInventory delivers a simple, reliable and productive user experience across a wide range of industries. The solution allows users to manage physical inventory movement in real-time and perform physical and cycle counts quickly while achieving greater accuracy of inventory levels. The precise tracking and paperless management of mInventory helps you to increase productivity, lower costs, optimize your supply chain, all while improving customer service.
To find out more about mServiceOrder, mInventory, or any of Innovapptive’s Mobile Workforce Management Solutions, our Solution Experts are ready to chat with you or you can reach us at (713) 275-1804.
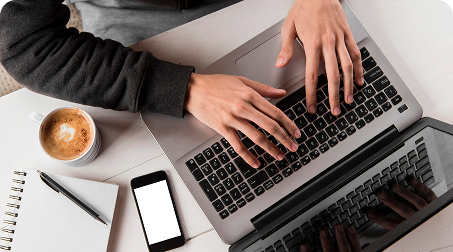
See It In Action
Schedule a personalized demo to see how our solutions can help your business thrive.
- 22-04-2025
The $3.6B Unlock: Solving the Chemical Industry’s Labor Crisis and EBITDA Pressure in One Move
“Constraints don’t slow innovation—they force it.”
- 21-04-2025
Chemical Industry's Margin Erosion: A Wake-Up Call for Operational Efficiency Amid China's Oversupply
The global chemical industry is facing mounting challenges, with revenue declines and shrinking...
- 21-04-2025
Why Wrench Time Isn’t Improving: The Hidden Costs of Traditional Maintenance Scheduling
For years, industrial leaders have relied on a common but flawed assumption: "Better planning and...