S/4HANA and Frontline Worker Integration Strategies for Operational Excellence in the Chemical Industry
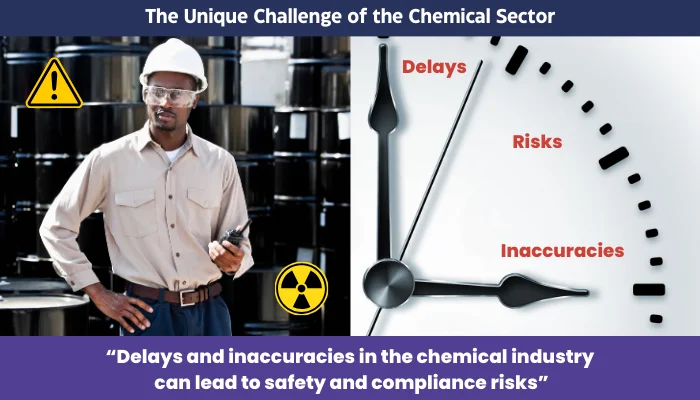
In the chemical industry, the need for operational efficiency, data accuracy, and compliance is accentuated due to the complexity and regulatory environment of the operations. Here’s an in-depth look at how businesses in this sector can significantly benefit from integrating S/4HANA with frontline technologies.
Introduction
The chemical industry is characterized by its intricate processes, stringent safety protocols, and the imperative for precision. S/4HANA, with its robust features, serves as an ideal ERP solution for addressing these complexities. However, the key to unlocking its full potential lies in seamless integration with frontline worker solutions.
The Unique Challenge
In the chemical sector, frontline workers engage in intricate, hazardous, and highly regulated activities. Information delay or inaccuracies aren’t just inefficiencies but potential safety and compliance risks. The real-time, accurate data processing capabilities of S/4HANA can be a game-changer, but only if they’re made accessible to the frontline.
Mobilizing S/4HANA
Here, mobile solutions tailored for the chemical industry play a pivotal role. By providing field workers with mobile tools for efficient work order execution, inventory transactions, and shift rounds, immediate data entry into the S/4HANA system is enabled. This real-time integration minimizes data lags, ensuring timely and informed decisions, crucial in the fast-paced and high-stakes chemical environment.
Safety and Compliance
The seamless data flow ensures that safety protocols are updated in real-time, and compliance is continuously monitored. In an industry where safety and regulatory adherence are paramount, this real-time data integration ensures that standards are not just met but exceeded, minimizing risks and potential fines.
Tangible Benefits
- Proactive Maintenance: In the chemical industry, asset maintenance is not just about efficiency but safety. Real-time data ensures immediate action, reducing the risk of breakdowns and hazards.
- Inventory Accuracy: Accurate real-time inventory data is crucial to avoid overstocking of hazardous materials or understocking, leading to operational delays.
- Operational Excellence: With immediate data entry, operators can focus on core activities, enhancing productivity and safety.
Future-Proofing Chemical Operations
Integration of S/4HANA with tailored frontline worker solutions ensures the chemical industry is equipped to adapt to evolving regulations, technologies, and operational challenges. It’s not just about digital transformation but about building a resilient, adaptable, and efficient operational framework that stands the test of time.
Conclusion
In the chemical industry, the integration of S/4HANA with frontline worker solutions is a strategic necessity. It ensures that the precision, real-time data, and efficiency capabilities of the ERP system are leveraged to their fullest, turning them into tangible operational benefits – efficiency, safety, and compliance. As the industry evolves, this integration will be the cornerstone of operational excellence, setting the benchmark for efficiency and safety in the complex, dynamic landscape of chemical operations.
By making S/4HANA accessible to the frontline in real-time, chemical companies can transcend traditional operational challenges, ushering in an era of unprecedented efficiency, safety, and compliance.
S/4Hana FAQs
Chemical plant frontline workers struggle with issues like manual data entry, isolated information, delayed feedback, tool and part searches, repetitive work, skill gaps, and safety. Although S/4HANA streamlines processes, its effectiveness is restricted with manual methods. Integrating S4/HANA with a third-party, mobile-first connected worker solution creates a link between frontline and back-office teams, improving execution, real-time visibility, and unity across operations, maintenance, and storeroom roles. This digital integration boosts communication, collaboration, and productivity, helping frontline workers overcome these challenges.
Integrating a mobile-first connected worker solution enhances safety standards and regulatory compliance in digital documentation and tracking. It allows frontline workers to perform accurate digital operator rounds and safety inspections, automatically submitting data to back-office systems, eliminating manual errors and delays. Supervisors and managers can monitor progress in real time, enabling swift remedial actions and resolutions for any safety or compliance issues detected.
Implementing an integrated frontline worker solution in the chemical industry brings several key benefits:
- Proactive Maintenance: Real-time data enables immediate action, reducing the risk of breakdowns and improving safety.
- Inventory Accuracy: Ensures optimal stock levels, preventing overstocking of hazardous materials and avoiding operational delays due to understocking.
- Operational Excellence: Immediate data entry allows operators to concentrate on primary tasks, increasing productivity and safety.
- Boosted Productivity: Automation and efficient workflows enable workers to achieve more in less time.
- Cost Efficiency: Digitization reduces contractor expenses, leading to long-term savings.
- Safety and Compliance: The system ensures adherence to safety protocols and compliance standards, minimizing potential liabilities.
Integration of S/4HANA with tailored frontline worker solutions ensures the chemical industry is equipped to adapt to evolving regulations, technologies, and operational challenges. It’s not just about digital transformation but about building a resilient, adaptable, and efficient operational framework that stands the test of time.
Yes, click here to see an example.
Innovapptive's connected worker platform offers intuitive, quick, and easy self-customization for superusers through its patented low-code/no-code technology. Users don't need coding skills to tailor applications to specific business needs, roles, or locations. The platform facilitates easy configuration for various applications and use cases, including operator rounds, equipment and safety inspections, planning and scheduling, work order execution, work instructions, warehouse management, and fixed asset reconciliation and tracking.
Yes. Integration offers real-time safety updates and notifications to field workers and managers, helping each make better decisions and take faster remedial action, reducing the risks and potential costs of an accident or non-compliance.
The seamless data flow from the connected worker platform to S4/HANA ensures that the backend ERP is continually updated with accurate, real-time data. This accuracy is instrumental in measuring precise KPIs, offering insights for informed decisions and continuous improvement. Exceptional work order management, improved inventory accuracy, and optimized operator efficiency become measurable outcomes of this integration.
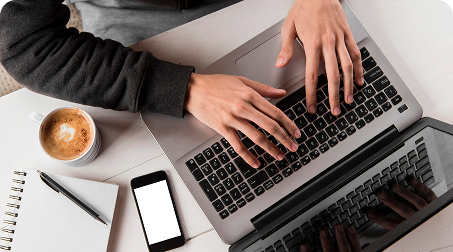
See It In Action
Schedule a personalized demo to see how our solutions can help your business thrive.
- 20-08-2025
Building the future of Industrial Operations with Innovapptive and AWS
Most manufacturers have already gone digital. Yet business outcomes haven’t moved in step. Many...
- 22-04-2025
The $3.6B Unlock: Solving the Chemical Industry’s Labor Crisis and EBITDA Pressure in One Move
“Constraints don’t slow innovation—they force it.”
- 21-04-2025
Chemical Industry's Margin Erosion: A Wake-Up Call for Operational Efficiency Amid China's Oversupply
The global chemical industry is facing mounting challenges, with revenue declines and shrinking...