SAP Mobile Transformation: RFID and Bar Code Peripheral Solutions for Smart Phones and Tablets are revolutionizing automatic data capture and processing in SAP
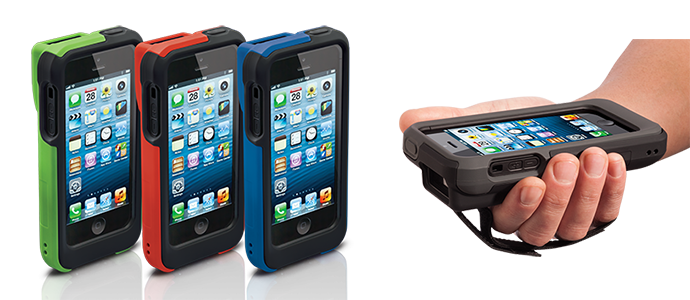
Implementing a mobile handheld device to automate and process your SAP transactions can be an expensive and complex affair. Automating critical SAP transactions such as work orders, inventory management or a point of sale solution require the ability to scan bar code through a mobile handheld device. However, these mobile handheld devices can be an extremely expensive proposition with devices ranging anywhere between $2000 - $6500, depending on your configuration and requirement with associated complex infrastructure to support offline requirements. A cost-complexity-benefit case analysis has traditionally limited the use of handheld devices to automate critical business locations, users and SAP transactions. However with the advent of smart phones, tablets and secured bring-your-own-device (BYOD) policies, your employee’s smart phones or corporate owned devices can be converted into handheld devices using disruptive RFID peripherals. These RFID peripherals now provide the ability to further automate SAP transactions that fell through the cracks in your cost-complexity-benefit case analysis of a handheld device.
What is an RFID/Bar Code Scanning Peripheral?
Companies such as Infinite Peripherals are redefining the mobile handheld devices by simply converting your smart phone or tablets into bar code scanning devices to assist processing automation of your SAP data.
Handheld vs. RFID/Barcode Peripheral Comparison Matrix
Compatible Mobile RFID and Bar Code Peripheral Solutions
Innovapptive’s offers several pre-built, SAP certified mobile solutions that run with these RFID and Bar Code Peripheral Solutions. Several of our Fortune 500 customers are using these devices to transform and automate a variety of their use cases. I have listed few examples below:
Mobile Quality Management
Innovapptive’s mQuality mobile solution allows quality managers to create SAP quality notifications in real-time in plants, warehouses and inventories. Capturing product defect details and images using their mobile device integrated with RFID peripherals is much easier in asset intensive industries. The recorded information is then assigned to a coordinator for faster processing of the defect resolution, thereby improving product quality and customer satisfaction.
Mobile Asset Tagging
Innovapptive's mAssetTag solution allows automation of your fixed asset physical inventory reconciliation by simply scanning fixed assets using these peripherals and using the smart phones GPS functionality to record it’s most current location to meet regulatory requirement of completing a 20% reconciliation of your fixed assets.
Mobile Inventory and Warehouse Management
Innovapptive’s mInventory solution uses RFID peripheral to automate critical inventory transactions such as inventory cycle counting, goods receipts, goods issue and stock look ups, resulting is accurate and up to date inventory information in SAP. With mPower™ mInventory mobile app, precise tracking and paperless management of inventory helps you increase productivity, lower costs, optimize your supply chain, and improve customer service.
Mobile Sales Execution
Innovapptive’s mSalesExec solution allows Sales reps need access to SAP CRM to have up to date information on the in-store placement which may be remotely located. The app is integrated with RFID/Bar Code peripherals to automate sales order creation by simply scanning SKU’s within an order guide to quickly create a sales order.
Mobile Work Order
Innovapptive’s mWorkOrder mobile solution is integrated with RFID devices allowing companies to share work order information with service and maintenance technicians in real time to help them get organized, record start and end time, review detailed work order information, analyze service routes, record notes, add components and upload relevant pictures and documents.
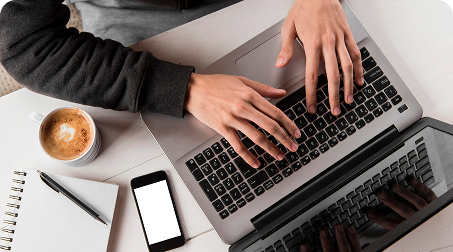
See It In Action
Schedule a personalized demo to see how our solutions can help your business thrive.
- 22-04-2025
The $3.6B Unlock: Solving the Chemical Industry’s Labor Crisis and EBITDA Pressure in One Move
“Constraints don’t slow innovation—they force it.”
- 21-04-2025
Chemical Industry's Margin Erosion: A Wake-Up Call for Operational Efficiency Amid China's Oversupply
The global chemical industry is facing mounting challenges, with revenue declines and shrinking...
- 21-04-2025
Why Wrench Time Isn’t Improving: The Hidden Costs of Traditional Maintenance Scheduling
For years, industrial leaders have relied on a common but flawed assumption: "Better planning and...