Struggling to Improve Wrench Time?
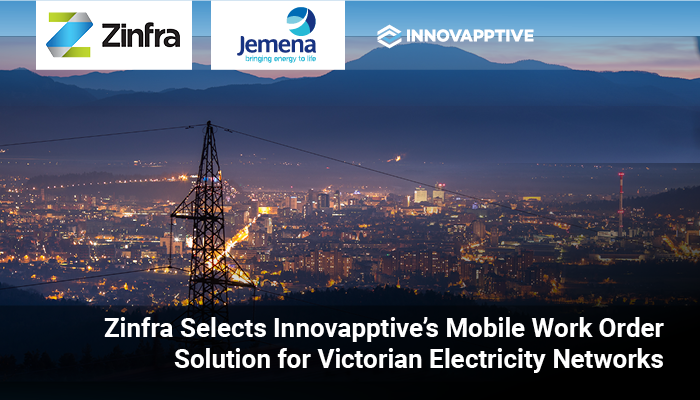
When maintenance technicians perform well it has a tremendous impact on the organization’s proficiency to optimize its production system and meet its long-term objectives. Maintenance technicians with higher wrench times would able to repair equipment and machines faster to help their organizations to start/restart their production and increase production. As a result, organizations can secure a competitive advantage and increase revenue & profit.
According to a study by the Aberdeen Group, organizations utilizing work order optimizations and mobile solutions for plant maintenance see performance gains such as a 28% increase in completed work orders, an 11% jump in first-call resolution rate, and a 16% reduction in late work orders completions, per day per technician.
Active maintenance planning and scheduling, a crucial aspect of maintenance management, help organizations to improve their wrench time. By optimizing the utilization of your maintenance crews (schedulers, planners, technicians, and operators), ineffective procedures are eliminated from the current practices. By equipping crews with the right technology solution, organizations can fully enhance their maintenance productivity and effectively manage maintenance tasks.
According to the Aberdeen Group study, organizations running truly optimized service schedules had, on average, improved work orders by 20% and increased “wrench time” by 18% completed per day per technician.
If you’re interested in measuring wrench time, increasing production, and implementing predictive maintenance, find your optimal wrench time solution with Innovapptive’s Connected Workforce Platform and mWorkOrder.
Improving Maintenance Productivity with Mobile Plant Maintenance
Innovapptive's mWorkOrder – Mobile Plant Maintenance solution, offered within our next generation Connected Workforce Platform, provides your maintenance technicians/workers anytime, anywhere access to the right information they need to do their jobs. mWorkOrder enables your workers to work safer, smarter, and more productively. mWorkOrder‘s barcode scanning features allow field technicians, supervisors, planners to automate searching for parts, equipment, and history of equipment to maximize your wrench time and support predictive maintenance efforts.
Using mWorkOrder, your supervisors can track performance and the start/stop times of technicians with the online/offline capabilities offered within mWorkOrder and assign work orders to technicians nearby. Your planners/schedulers can create, update, and view maintenance plans in real-time and see where assets are located, accordingly. With the right information and work instructions, your maintenance technicians’ productivity will increase – more completed work orders in a day result in improved wrench time and effective maintenance management.
Learn how a leading Australian Utility company partnered with Innovapptive to implement mWorkOrder with RACE™ Dynamic Forms. The results optimized their maintenance planning, improved their assets' reliability, and are saving field workers time while allowing them to work on the go with real-time updates and proactive predictive maintenance capabilities.
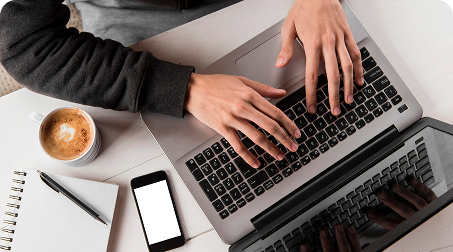
See It In Action
Schedule a personalized demo to see how our solutions can help your business thrive.
- 20-08-2025
Building the future of Industrial Operations with Innovapptive and AWS
Most manufacturers have already gone digital. Yet business outcomes haven’t moved in step. Many...
- 22-04-2025
The $3.6B Unlock: Solving the Chemical Industry’s Labor Crisis and EBITDA Pressure in One Move
“Constraints don’t slow innovation—they force it.”
- 21-04-2025
Chemical Industry's Margin Erosion: A Wake-Up Call for Operational Efficiency Amid China's Oversupply
The global chemical industry is facing mounting challenges, with revenue declines and shrinking...