Tracking Wrench Time and Cutting Labor Costs with a Mobile Plant Maintenance Solution
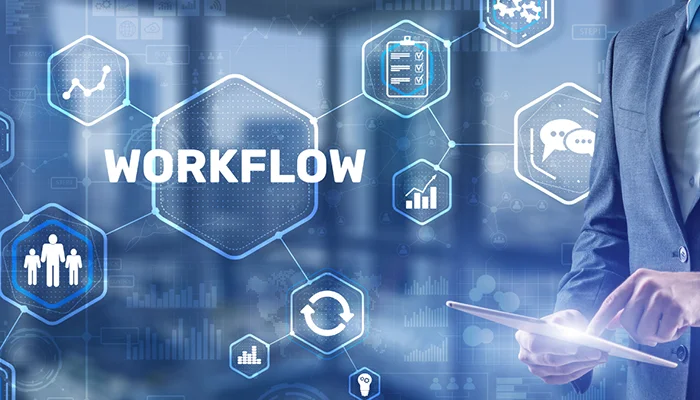
Inefficient maintenance operations can wreck a plant’s budget and put a serious crimp on production, revenues and profit margins. But that’s not all. Maintenance departments that lack visibility into technicians’ wrench time face serious problems with work order management, resource allocation, backlogs and unplanned downtime. Those problems are multiplied when a plant uses a run-to-fail maintenance program and manual, paper-based systems to track time and work order progress.
It doesn’t have to be this way… not anymore. Digital transformation and mobile plant maintenance applications such as connected worker platforms offer a ladder out of this ever-deepening money pit.
Earlier in this series, we asked Companies Confront Higher Downtime Costs; Can Mobile Plant Maintenance Offer a Solution? and discussed Accurately Capturing Wrench Time Key to Lowering Plant Maintenance Costs. If you haven’t already read these earlier blogs, be sure to click the links to do so. In this final blog, let’s examine how one such solution empowers maintenance managers to better track wrench time to boost productivity, lower labor costs and eliminate the need for expensive outside contractors.
The mWorkOrder Mobile Plant Maintenance Solution
Innovapptive’s mWorkOrder delivers real-time visibility into the plant maintenance process. This enterprise asset management application works with consumer-grade or industrial rugged mobile devices (smartphones, tablets, etc.) to provide anywhere/anytime access to information, features and support.
Using mWorkOrder, technicians can accurately record time spent executing work orders in the field. Time data automatically uploads into SAP, IBM Maximo or CATS time sheets and is available for immediate viewing and analysis.
The mWorkOrder mobile plant maintenance solution offers four major advantages:
- Cut out workflow inefficiencies: Managers gain greater insight and understanding into how their technicians are spending their time. This gives them the data they need to formulate more efficient work processes.
- Raise productivity: More efficient work order processes decrease time wasted on non-productive tasks, thus increasing wrench time and enabling more actual work to get accomplished in a day.
- Decrease labor costs: Greater technician productivity results in less overtime or a need to employ expensive outside contractors to supplement in-house staff.
- Eliminate paperwork: Record and track time in seconds with just a few simple clicks. No more paper timesheets to fill out or upload into a back-office system.
What Separates mWorkOrder from the Rest of the Field
Innovapptive’s mission is a simple one: to connect and create conversations between people, machinery and work processes, and to improve people’s lives. To accomplish that, we’ve ensured that mWorkOrder has several attributes that differentiate it in the marketplace, such as:
- Seamlessly integrates with SAP and IBM Maximo
- Ready to deploy out-of-the-box
- Simple and intuitive to use
- Code-free personalization of site, role, user and geographies
- Collaborate anywhere, anytime
- Works in online and offline modes
- Enterprise-grade security
See a Free Demo of mWorkOrder in Action Today
Innovapptive offers the only connected worker platform that digitizes the last mile of frontline workers into SAP and IBM Maximo. We can empower you to reimagine your operations and save millions of dollars on maintenance costs. Schedule a free demo of our world-class mWorkOrder, then call 888-464-6668 to speak to our industry experts. They’ll be happy to answer your questions, help you calculate downtime costs and return on investments, identify opportunities for efficiencies and savings, and explain how mobile plant maintenance can benefit you.
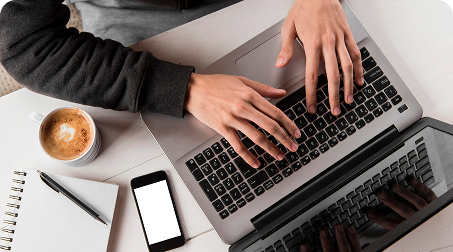
See It In Action
Schedule a personalized demo to see how our solutions can help your business thrive.
- 20-08-2025
Building the future of Industrial Operations with Innovapptive and AWS
Most manufacturers have already gone digital. Yet business outcomes haven’t moved in step. Many...
- 22-04-2025
The $3.6B Unlock: Solving the Chemical Industry’s Labor Crisis and EBITDA Pressure in One Move
“Constraints don’t slow innovation—they force it.”
- 21-04-2025
Chemical Industry's Margin Erosion: A Wake-Up Call for Operational Efficiency Amid China's Oversupply
The global chemical industry is facing mounting challenges, with revenue declines and shrinking...