What MRO Inventory Metrics Should You Track?
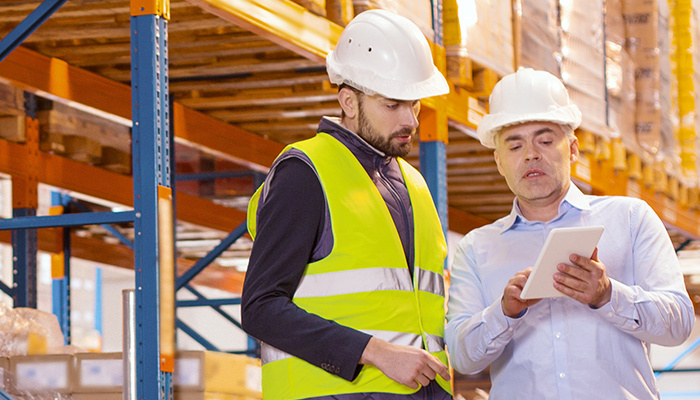
Key Takeaways
- Tracking MRO Metrics Improves Efficiency: Monitoring metrics like inventory accuracy, order lead time, and stockout rate reduces downtime, prevents bottlenecks, and ensures timely resource allocation.
- Innovapptive’s Warehouse Dashboard Delivers Real-Time Insights: With real-time tracking, KPI alerts, and data-driven insights, Innovapptive’s dashboard helps organizations make quick decisions and improve operational efficiency.
Introduction
Warehouse operations are the backbone of efficient supply chain management, directly impacting overall business performance through the accuracy and timeliness of processes. However, many organizations struggle to optimize key metrics within their warehouse operations, leading to inefficiencies and financial losses.
Recent data from an Innovapptive’s internal dashboard highlights several critical areas requiring immediate attention, including Inventory Accuracy, Loss Due to Inaccuracy, and Average Order Lead Time. These metrics are currently underperforming, with Inventory Accuracy at 71% (below the target of over 83%), losses due to inaccuracy at $78,991 (far exceeding the goal of under $1,999), and an Average Order Lead Time of 7 minutes, more than double the target of 3 minutes.
Survey data from the The State of Digital Manufacturing 2025 report reinforce the importance of focusing on inventory optimization. According to the report, 57.5% of manufacturing companies struggle with equipment downtime, which directly affects inventory management, leading to unplanned stockouts and overstocking. Additionally, 60% of survey respondents identified inventory inaccuracies as a major contributor to operational inefficiencies. Companies experiencing inventory issues often face higher costs tied to emergency orders, excessive carrying costs, and lost sales opportunities.
Additionally, according to the Siemens: The True Cost of Downtime 2022 report, unplanned downtime costs Fortune Global 500 companies approximately $1.5 trillion annually, with inventory-related inefficiencies being a key factor. On average, automotive manufacturers face $2 million in downtime losses per hour, leading to annual losses of $2.4 billion.
These inefficiencies not only disrupt operational performance but also translate into significant financial setbacks. Addressing these gaps through strategic interventions and leveraging advanced analytics can drive substantial improvements in warehouse efficiency. By focusing on these key metrics, organizations can improve their operational workflows, reduce costs, and better meet customer expectations, ultimately strengthening their competitive position in the market.
The Benefits of Effective Metric Tracking
Effective tracking of Maintenance Repair Operations (MRO) inventory metrics offers several advantages:
- Enhanced Efficiency: Real-time monitoring of key metrics like inventory accuracy and order lead time helps streamline operations, reducing wasted time and resources. Immediate adjustments based on data prevent bottlenecks and keep processes running smoothly.
- Cost Reduction: By leveraging Digital Warehouse Solutions to track inventory levels, businesses avoid overstocking and understocking, minimizing unnecessary spending. Managing metrics like obsolescence and inactive stock also reduces costs tied to holding outdated or excess inventory.
- Improved Decision-Making: Data-driven insights from metric tracking enable more informed decisions. With a clear view of performance trends, managers can optimize inventory levels, forecast demand accurately, and align operations with strategic goals.
13 Key Metrics to Track for MRO Inventory Optimization
To drive operational efficiency in Maintenance Repair Operations (MRO) and warehouse management, it's essential to focus on a few critical MRO inventory metrics. These metrics offer valuable insights into inventory management, supply chain responsiveness, and overall warehouse performance. By tracking these key indicators, organizations can quickly identify inefficiencies, reduce costs, and ensure that operations align with business objectives. Prioritizing the right metrics allows for more strategic decision-making and helps maintain a competitive edge in the market.
Here are the key metrics to track:
- Inventory Accuracy: Inventory accuracy measures the alignment between recorded and actual inventory levels. Maintaining a high accuracy rate (above 99%) is vital for avoiding over-ordering and stockouts, ensuring that warehouse operations run smoothly. Accurate inventory records are foundational to effective warehouse management. They prevent disruptions by ensuring that necessary parts are available when needed, minimizing downtime and enhancing operational flow.
Inventory accuracy is a critical metric that measures how closely physical inventory matches recorded data. A current accuracy rate of 71% is significantly below the industry standard and internal target of 83%, suggesting discrepancies that can lead to stockouts, overstocking, and ultimately, lost revenue. - Stockout Rate: Stockout rate tracks the frequency of running out of critical inventory items. A low stockout rate (ideally under 1%) is crucial for maintaining operational continuity and avoiding costly delays. Stockouts can severely disrupt operations, leading to increased costs due to emergency purchases and expedited shipping. Managing stockout rate involves proactive inventory management and demand forecasting.
Techniques for Effective Monitoring:
- Safety Stock Levels: Maintain buffer stock for high-demand items.
- Automated Alerts: Use inventory management systems to set reorder alerts.
- Regular Reviews: Continuously analyze inventory levels and adjust reorder points accordingly.
- Carrying Cost of Inventory: Carrying cost refers to the total expense of holding inventory, including storage, insurance, and opportunity costs. High carrying costs indicate inefficiencies and can strain financial resources. Excessive carrying costs can tie up capital that could be better used elsewhere in the business, leading to reduced financial flexibility and increased risk.
Minimizing Carrying Costs through Strategic Management:
- Inventory Optimization: Balance inventory levels to meet demand without overstocking.
- Demand Forecasting: Use data-driven approaches to predict future inventory needs accurately.
- Reducing Slow-Moving Stock: Regularly review inventory to identify and minimize slow-moving items.
- Average Order Picking Time: Order picking is a critical warehouse operation that directly impacts order fulfillment speed and labor costs. Reducing average order picking time can lead to faster delivery times and improved customer satisfaction. Advanced technologies such as warehouse management systems (WMS) and automated guided vehicles (AGVs) can significantly reduce order picking times by streamlining workflows and reducing manual labor.
Best Practices for Reducing Picking Time:
- Optimized Warehouse Layout: Design the layout to minimize travel time and improve workflow efficiency.
- Use of Technology: Implement pick-to-light systems and automated picking solutions.
- Process Improvement: Continuously refine picking processes based on performance data.
- Average Putaway Turnaround Time: Putaway turnaround time measures how quickly received goods are stored in their designated locations. Efficient putaway processes ensure that inventory is available for picking sooner, reducing bottlenecks and improving overall warehouse flow. Innovative tools such as mobile putaway applications and real-time inventory tracking can significantly enhance putaway efficiency, leading to faster order fulfillment and reduced operational costs.
Optimizing Putaway Processes:
- Automation: Utilize AGVs and conveyor systems for faster putaway.
- Real-Time Tracking: Implement systems that track putaway activities in real-time to monitor performance and identify areas for improvement.
- Layout Design: Ensure that the warehouse layout supports efficient putaway by minimizing travel distances and optimizing storage locations.
- Days Inventory on Hand (DIH): Days Inventory on Hand (DIH) measures the average number of days inventory is held before it is used or sold. Managing DIH effectively is critical for maintaining optimal inventory levels and minimizing holding costs. Warehouse management systems and analytics tools monitor DIH in real-time, making adjustments as needed to maintain efficiency and reduce costs.
Setting and Maintaining Optimal DIH Levels:
- Regular Monitoring: Continuously track DIH to ensure it stays within the desired range.
- Inventory Segmentation: Segment inventory based on demand and adjust DIH targets accordingly.
- Just-In-Time Inventory: Implement just-in-time (JIT) strategies to reduce DIH and improve cash flow.
- Order Accuracy: Order accuracy refers to the percentage of orders fulfilled correctly without errors. High order accuracy is crucial for maintaining customer satisfaction and reducing returns.
Strategies for Ensuring High Accuracy Rates:
- Automated Order Processing: Use technology to automate order processing and reduce human errors.
- Quality Control: Implement quality control checks at multiple stages of the fulfillment process.
- Employee Training: Ensure that warehouse staff are trained in best practices for order picking and packing.
- Order Lead Time: Order lead time measures the time taken from placing an order with a supplier to receiving the goods. Reducing lead time is essential for improving operational agility and responsiveness. Shorter lead times enable warehouses to respond more quickly to changes in demand, reducing the risk of stockouts and overstocking.
- Fill Rate: Fill rate measures the percentage of customer orders that are fulfilled from available stock. A high fill rate is indicative of good inventory management and contributes to customer satisfaction.
- Inventory Turnover Rate: Inventory turnover rate indicates how many times inventory is sold or used over a specific period. Higher turnover rates suggest efficient inventory management, while lower rates may indicate overstocking or slow-moving items.
Improving Turnover for Better Efficiency:
- Demand Planning: Accurately forecast demand to align inventory levels with market needs.
- Inventory Reduction: Regularly review inventory levels and reduce slow-moving stock.
- Supply Chain Optimization: Work closely with suppliers to optimize order quantities and delivery schedules.
- Emergency Supply Costs: Emergency supply costs refer to the expenses incurred due to unplanned or urgent purchases. Managing these costs is crucial for maintaining budget control and preventing disruptions in operations.
Strategies for Predictive Inventory Management:
- Predictive Analytics: Use data to predict potential supply disruptions and plan accordingly.
- Supplier Relationships: Build strong relationships with suppliers to ensure quick responses during emergencies.
- Inventory Buffers: Maintain strategic inventory buffers for critical items to reduce reliance on emergency purchases.
- Obsolescence Rate: Obsolescence rate measures the percentage of inventory that is no longer usable or sellable. High obsolescence rates can lead to significant financial losses and wasted storage space. Excessive obsolete inventory ties up capital and can result in write-offs, impacting the bottom line. Managing obsolescence through regular inventory reviews and strategic liquidation can mitigate these risks.
- Inactive Stock: Inactive stock refers to inventory that has not been used for a specified period. Managing inactive stock is crucial for optimizing warehouse space and reducing holding costs.
Strategies for Reducing Inactive Stock:
- Inventory Rotation: Regularly rotate stock to prevent items from becoming inactive.
- Inventory Audits: Conduct regular audits to identify and address inactive stock.
Innovapptive’s Dashboard: Precision Tracking for Operational Excellence
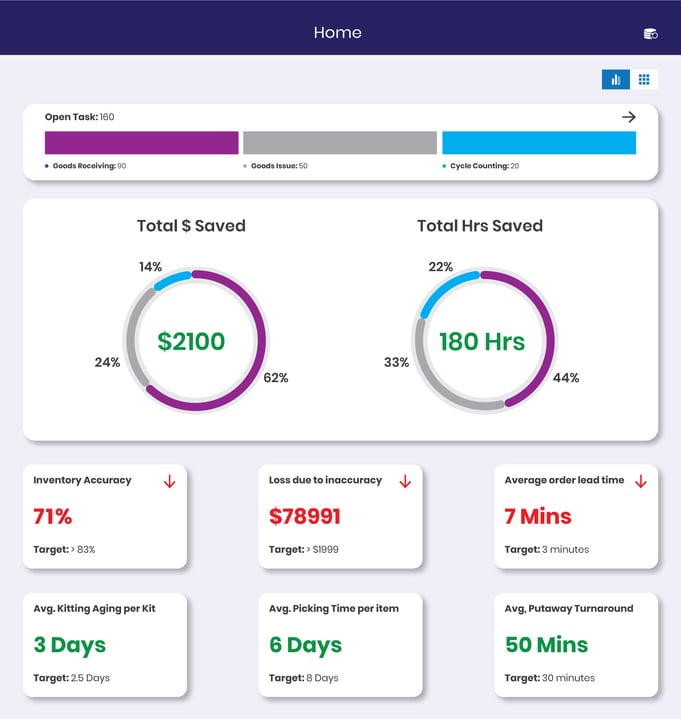
A comprehensive Warehouse Performance Dashboard provides critical oversight into warehouse operations by tracking key performance indicators (KPIs) such as inventory accuracy, order lead time, average order picking time, and putaway turnaround time. By enabling organizations to monitor these metrics in real-time, dashboards play a pivotal role in identifying inefficiencies, optimizing workflows, and reducing operational costs.
Innovapptive’s Warehouse Performance Dashboard builds on these capabilities, offering a powerful tool for tracking and managing warehouse KPIs. It goes beyond basic tracking by providing features such as:
- Real-Time Task Management: Assign and monitor tasks dynamically to ensure optimal resource utilization and smooth operations.
- KPI Alerts: Continuous monitoring with customizable alerts for quick response to deviations in critical metrics.
- Data-Driven Insights: Visualizations and analytics provide actionable insights, enabling informed decision-making and improved efficiency.
- Operational Efficiency: Streamline workflows and reduce processing times through real-time monitoring and corrective actions.
- Accuracy and Cost Reduction: Maintain accurate inventory records to minimize discrepancies, stockouts, and overstocking, leading to cost savings.
Conclusion
Monitoring and managing key Maintenance Repair Operations (MRO) inventory metrics is essential for optimizing warehouse operations. By focusing on these metrics, organizations can achieve greater efficiency, reduce costs, and improve overall operational performance.
Implementing the right tools and strategies, such as Innovapptive’s Warehouse Performance Dashboard, can transform your warehouse operations. By making data-driven decisions and continuously monitoring KPIs, businesses can stay competitive and meet the demands of the modern market.
Explore more about how advanced tools can drive your warehouse efficiency to new heights. Schedule a free demo today to learn more.
FAQs
What is the significance of inventory accuracy in MRO operations?
Inventory accuracy ensures that the recorded stock levels align with the actual stock, preventing overstocking, stockouts, and disruptions in operations.
How can Innovapptive’s Warehouse Dashboard improve our operational efficiency?
The dashboard offers real-time task management, KPI alerts, and visual analytics, helping organizations optimize workflows and reduce errors.
What is the role of stockout rate in warehouse management?
The stockout rate measures the frequency of running out of critical parts. A low stockout rate ensures smooth operations, avoiding delays and emergency orders.
How does tracking the carrying cost of inventory benefit businesses?
Tracking carrying costs helps reduce unnecessary expenses related to holding excess inventory, such as storage and insurance costs, improving financial flexibility.
What strategies can reduce emergency supply costs?
Predictive analytics, maintaining strategic inventory buffers, and developing strong supplier relationships can help minimize emergency purchases and associated costs.
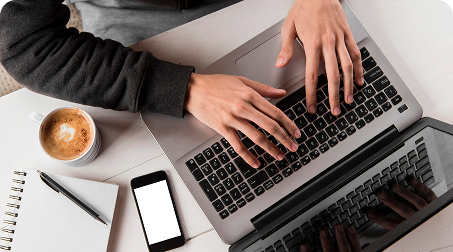
See It In Action
Schedule a personalized demo to see how our solutions can help your business thrive.
- 20-08-2025
Building the future of Industrial Operations with Innovapptive and AWS
Most manufacturers have already gone digital. Yet business outcomes haven’t moved in step. Many...
- 22-04-2025
The $3.6B Unlock: Solving the Chemical Industry’s Labor Crisis and EBITDA Pressure in One Move
“Constraints don’t slow innovation—they force it.”
- 21-04-2025
Chemical Industry's Margin Erosion: A Wake-Up Call for Operational Efficiency Amid China's Oversupply
The global chemical industry is facing mounting challenges, with revenue declines and shrinking...