10 Things to Consider When Choosing a SAP Mobile Plant Maintenance Solution
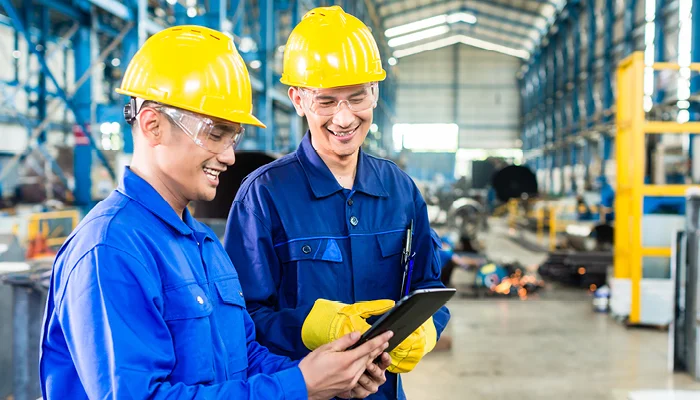
Industrial Challenges Facing Plant Managers
Industrial and manufacturing plant managers are increasingly challenged to accomplish more tasks with fewer resources, especially labor. Fortunately, technology offers a way to successfully answer such challenges, even when plants are finding it tougher to find and keep frontline workers. This blog will discuss the advantages and benefits of one such technology available today: the mobile plant maintenance solution tied to SAP Mobile PM. It will also offer 10 things to look for when choosing such a solution for your enterprise.
Common Plant Maintenance Problems
Do any of these plant maintenance problems sound familiar? Maintenance departments ensure equipment uptime, customer satisfaction, and steady revenue streams, but they frequently face six common issues:
- Unplanned asset downtime
- Work order management
- Manual data collection and entry
- Work order backlogs
- Productivity and wrench time
- Safety and regulatory compliance
Plants using a paper-based process are at a disadvantage when trying to overcome these problems:
- No real-time visibility
- Communication delays
- Greater chance for errors
- Non-value-added tasks
- Data gathering and sharing
- Manual entry into ERP
Paper-based work order processes lead to less effective reactive maintenance programs instead of preventive or predictive ones. Reactive or run-to-fail maintenance practices result in:
- Greater risks for equipment failure
- More safety incidents
- Additional revenue-draining downtime
- Worse customer service
A mobile plant maintenance solution empowers maintenance supervisors and frontline workers to prevail over obstacles that hinder efficiency, productivity, and rapid response to issues. How? We’ll cover that next.
A mobile plant maintenance solution empowers supervisors and frontline workers to overcome these obstacles, improving efficiency, productivity, and response times. Let’s explore how it works.
How a Mobile Plant Maintenance Solution Works
Frontline technicians and operators using mobile devices like smartphones, scanners, tablets, and wearables can fulfill maintenance work orders and perform inspections, operator rounds, and equipment checks via a specially designed mobile application. Operational data is automatically uploaded to SAP Mobile PM through the application—no need for paper forms or manual data entry. This transition to digital processes boosts wrench time and cuts administrative costs.
A mobile plant maintenance solution increases communication between field technicians and supervisors. Managers can create and issue digital work orders and follow the progress in real time. Supervisors instantly receive work order updates and can send push notifications to their employees’ mobile devices to notify them immediately of tasks or other information.
What to Look For In a Mobile Plant Maintenance Solution
Interested in the mobile plant maintenance solution concept? It offers a way to digitally transform your operations. There are many vendors today selling such applications. It’s a crowded marketplace. So how can you differentiate between them and select the right one for your company and its unique needs?
- Simple and user-friendly interface – A best-in-class mobile plant maintenance solution should deliver a simple, user-friendly interface. An easy-to-use application aids productivity and promotes greater user adoption, helping to justify the purchase.
- Hands-free operations - A best-in-class mobile plant maintenance platform should deliver voice-enabled work instructions on a tablet or a wearable device, such as smart glasses.
- Barcode scanning - This feature helps identify equipment history and helps search for parts. Another benefit is the geo-tagging feature that lets you pinpoint the exact location of the equipment - useful during tracking and auditing of assets. A best-in-class mobile plant maintenance platform should provide barcode scanning with the help of a camera available on a smartphone or a tablet, saving search time and avoiding information inaccuracies.
- Configurable risk matrix - A best-in-class mobile plant maintenance should include a configurable digital risk matrix. Mitigating threats and risks ensures continued production, longer asset life, greater compliance, and enhanced safety. A configurable risk matrix allows decision makers, planners, schedulers, and supervisors to prioritize mobile maintenance work orders based on the risk profile of all equipment throughout the facility. As the matrix is configurable, it can be altered to correspond to changing business conditions.
- Remote two-way video conferencing - Along with hands-free operations A best-in-class mobile plant maintenance platform needs to provide two-way video conferencing between a remote expert and frontline worker, integrated with ERP operational data and step-by-step work instructions.
- Guided work instructions - A best-in-class mobile plant maintenance solution should offer guided work instruction capabilities. This enables supervisors, experienced technicians, and subject experts to deliver digital guided work instructions to less-experienced frontline workers via two-way conferencing and hands-free devices such as smart glasses or visors. The expert can see what the technician sees from that person's point of view. This lets the two remotely collaborate and seamlessly share knowledge even though the two may be miles apart.
- Prepackaged digital forms library - A best-in-class mobile plant maintenance platform ought to provide a digital library of prepackaged work instructions, inspection forms, and compliance and safety procedures that frontline workers can access and use at any time, from anywhere. Workers can use these instructions and forms as is or managers and supervisors can reconfigure them as needed to meet changing business, operational, and compliance requirements.
- Search options - A best-in-class mobile plant maintenance platform should provide user-friendly search options for the availability and location of spare parts. This maximizes the user's efficiency while improving the repair timelines.
- Document viewing - A best-in-class mobile plant maintenance platform should provide access to work order instructions, technical documents, and safety instructions in a variety of formats, including PDF. This enables planners, schedulers, supervisors, and technicians to increase productivity, boost wrench time, improve communication, and make more informed decisions about work orders and assignments.
- Ability to upload pictures – Rather than typing endless text to describe the equipment, a best-in-class mobile application for plant maintenance should enable frontline workers to attach pictures associated with equipment breakdowns and work orders, improving communications and understanding.
Ten tips not enough for you? Here’s a bonus suggestion to keep in mind when evaluating the best mobile plant maintenance solution.
- Quick deployment - A best-in-class mobile plant maintenance solution should quickly adapt to an organization's infrastructure, enabling rapid deployment and minimizing implementation timelines.
See a Best-in-Class Mobile Plant Maintenance Solution Today
Innovapptive's mWorkOrder is a mobile plant maintenance solution that delivers all 11 items discussed here—and more. mWorkOrder supports preventive and predictive maintenance strategies and empowers maintenance teams to move away from a reactive, "run-to-fail" approach.
Watch a short two-minute introduction video here. Then, discover how mWorkOrder can transform your maintenance operations by scheduling a free demo or contacting one of our experts at 844-464-6668.
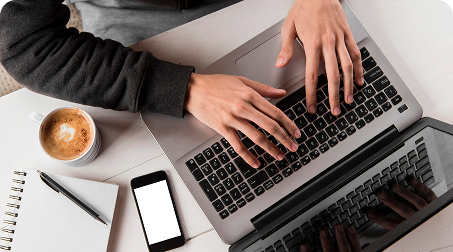
See It In Action
Schedule a personalized demo to see how our solutions can help your business thrive.
- 20-08-2025
Building the future of Industrial Operations with Innovapptive and AWS
Most manufacturers have already gone digital. Yet business outcomes haven’t moved in step. Many...
- 22-04-2025
The $3.6B Unlock: Solving the Chemical Industry’s Labor Crisis and EBITDA Pressure in One Move
“Constraints don’t slow innovation—they force it.”
- 21-04-2025
Chemical Industry's Margin Erosion: A Wake-Up Call for Operational Efficiency Amid China's Oversupply
The global chemical industry is facing mounting challenges, with revenue declines and shrinking...