Costly Disconnects in the Chemical Plant Preventative Maintenance Process
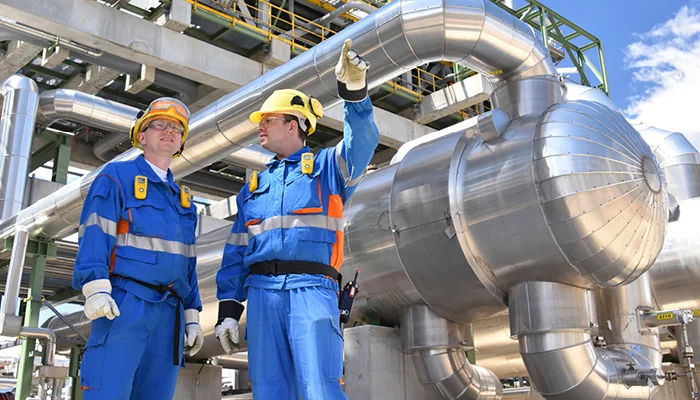
Chemical plants are high-risk environments where efficiency and safety are paramount. Yet, maintenance inefficiencies often lead to delays, downtime, and safety hazards. Research shows that up to 75% of an industrial craftsperson’s time is wasted on non-productive tasks, leaving only 25-35% devoted to actual maintenance work.
This inefficiency is costly for process manufacturing industries, leading to increased downtime, compliance risks, and higher operational costs. A significant reason behind these maintenance disconnects is outdated, paper-based processes that slow down work order execution, limit visibility, and create information silos.
This blog explores how preventative maintenance inefficiencies impact chemical plants, the root causes behind costly disconnects, and how digital transformation with mobile work order management solutions can increase efficiency, reduce costs, and improve safety.
The Hidden Costs of Preventative Maintenance Disconnects
Chemical plant maintenance is a complex, time-sensitive process. However, many maintenance teams struggle with inefficiencies due to manual workflows, disconnected systems, and lack of real-time visibility.
Where Is Time Wasted in Chemical Plant Maintenance?
-
Transitioning Between Tasks – Delays in receiving work orders, approvals, and material assignments.
-
Waiting for Instructions & Materials – Workers spend time looking for parts, tools, or documentation.
-
Paper-Based Processes – Supervisors rely on handwritten reports and manual data entry.
Fact: A lack of real-time visibility wastes valuable hours, leading to higher costs and increased safety risks.
Why Paper-Based Maintenance Processes Hurt Chemical Plants
Delayed Decision-Making & Lack of Real-Time Visibility
Paper-based processes create information silos, preventing decision-makers from accessing real-time maintenance data.
-
Supervisors lack real-time updates on maintenance progress.
-
Manual data entry delays maintenance scheduling.
-
Critical safety risks go unnoticed due to slow reporting.
Solution: A mobile maintenance management system allows instant updates and real-time visibility into work orders.
Increased Administrative & Labor Costs
Manual work orders require time-consuming data entry, increasing labor costs and administrative overhead.
-
High paperwork processing time slows operations.
-
Errors in manual data entry lead to incorrect maintenance actions.
-
Delayed work order completion results in unplanned downtime.
Solution: Digital work orders eliminate paperwork, speeding up approvals and reducing labor-intensive tasks.
Higher Safety Risks & Regulatory Compliance Challenges
Safety is a top priority in chemical plants, but paper-based safety checklists delay hazard identification.
-
Operators must wait for safety data to be recorded manually.
-
Safety incidents are not reported in real time.
-
Audits require time-consuming paperwork retrieval.
Solution: Mobile safety checklists and real-time reporting allow instant safety hazard identification, reducing compliance risks.
How Digitization Solves Preventative Maintenance Disconnects
Mobile Work Order Management for Chemical Plants
A mobile-first maintenance management system eliminates inefficiencies caused by paper-based workflows. Chemical plant operators and maintenance teams can execute work orders digitally using smartphones, tablets, and wearables.
💡 Key Benefits:
- Real-time Work Order Tracking – Supervisors receive instant updates on maintenance progress.
- Faster Work Order Approvals – Eliminate manual paperwork delays.
- Improved Communication – Push notifications keep maintenance teams informed in real time.
- Instant Access to Maintenance Data – Technicians can view instructions, checklists, and reports digitally.
Predictive Maintenance for Chemical Plants
Preventative maintenance is effective, but predictive maintenance offers greater efficiency.
-
IoT Sensors Monitor Equipment Performance – Detect anomalies before failures occur.
-
AI-Based Predictive Maintenance Models – Schedule maintenance only when necessary.
-
Automated Alerts for Equipment Health – Reduces unexpected failures and production downtime.
Result: Lower maintenance costs, fewer breakdowns, and improved uptime.
How Innovapptive's mWorkOrder Transforms Preventative Maintenance
Innovapptive’s mWorkOrder is a mobile-first connected maintenance solution that eliminates costly disconnects in chemical plant maintenance. It supports both preventative and predictive maintenance, allowing process manufacturers to move away from inefficient, reactive maintenance practices.
Key Features of mWorkOrder for Chemical Plants:
- Mobile Work Order Management – Assign, track, and complete work orders from anywhere.
- Real-Time Maintenance Visibility – Monitor maintenance progress instantly.
- Automated Safety & Compliance Reporting – Ensure regulatory compliance with digital safety checklists.
- IoT-Enabled Predictive Maintenance – Reduce downtime with data-driven maintenance planning.
- Offline Access for Remote Locations – Technicians can work without network connectivity.
Fact: Chemical plants that implement mobile maintenance solutions see up to 30% improvement in wrench time and a 25% reduction in downtime.
Ready to Eliminate Costly Maintenance Disconnects?
Stop relying on inefficient, paper-based maintenance workflows. Digitize your preventative maintenance process with Innovapptive’s mWorkOrder and boost operational efficiency, reduce downtime, and improve safety.
Get a Free Demo Today! 📞 Call 888-464-6668 to speak with our industry experts.
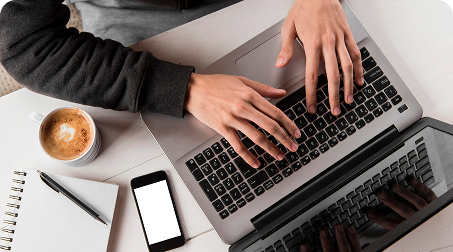
See It In Action
Schedule a personalized demo to see how our solutions can help your business thrive.
- 22-04-2025
The $3.6B Unlock: Solving the Chemical Industry’s Labor Crisis and EBITDA Pressure in One Move
“Constraints don’t slow innovation—they force it.”
- 21-04-2025
Chemical Industry's Margin Erosion: A Wake-Up Call for Operational Efficiency Amid China's Oversupply
The global chemical industry is facing mounting challenges, with revenue declines and shrinking...
- 21-04-2025
Why Wrench Time Isn’t Improving: The Hidden Costs of Traditional Maintenance Scheduling
For years, industrial leaders have relied on a common but flawed assumption: "Better planning and...