Equipment Dashboard: Actionable Asset Data for Optimal Plant Maintenance Management
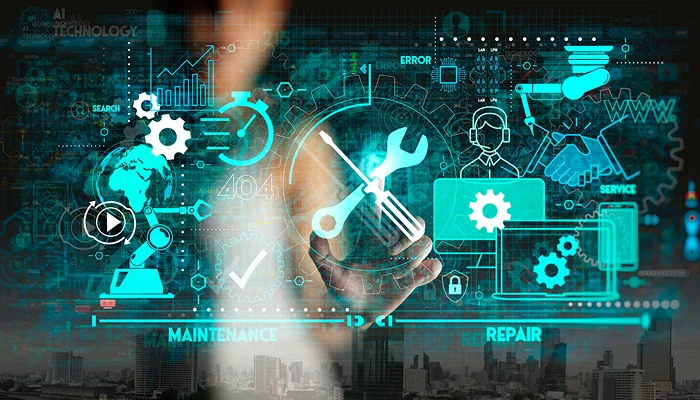
With advancements in technology, the quality of equipment data has improved as industries transition from traditional FAT files to sophisticated enterprise resource planning (ERP) systems like SAP and enterprise asset management (EAM) solutions such as IBM Maximo. However, these solutions still pose accessibility challenges for frontline workers and maintenance teams. Innovapptive’s mobile plant maintenance solution addresses these challenges, empowering teams to boost productivity, optimize asset management, and enhance profitability.
Challenges with Traditional ERP and EAM Systems
ERP and EAM systems are often confined to back-office operations, leaving frontline teams reliant on outdated, paper-based methods to access crucial data. Fragmented and incomplete access to asset data leads to uninformed decision-making, inefficient maintenance planning, and missed optimization opportunities. In the era of digital transformation, it is essential to bridge these gaps for seamless plant maintenance management.
Innovapptive’s Mobile Plant Maintenance Solution: Real-Time Asset Data at Your Fingertips
Innovapptive’s mobile plant maintenance management solution, integrated with SAP PM and IBM Maximo, features an interactive asset dashboard accessible on mobile devices. With a simple scan, frontline workers and maintenance managers can view comprehensive, real-time asset information, including asset descriptions, locations, warranty details, equipment hierarchies, manufacturer specifications, maintenance histories (breakdowns, work orders, and notifications), and scheduled tasks.
Easy access to real-time data on the shop floor empowers technicians and maintenance managers to make timely and informed decisions, reducing equipment downtime and enhancing operational efficiency. The dashboard includes key performance metrics like Mean Time to Repair (MTTR) and Mean Time Between Failures (MTBF), enabling companies to boost asset reliability, improve Overall Equipment Effectiveness (OEE), and optimize predictive maintenance efforts.
Meeting the Challenges of Workforce Attrition and Knowledge Gaps
The industrial sector faces workforce attrition known as the "Great Crew Change," where experienced technicians are retiring, and millennials and Gen Z are entering the workforce with limited exposure to established practices. Younger technicians lack access to the "tribal knowledge" built over years by retiring experts, leading to potential operational inefficiencies.
Innovapptive’s solution facilitates seamless knowledge transfer by enabling real-time asset updates through an intuitive mobile interface. Technicians can now perform their duties with confidence, using reliable, accessible data on equipment histories and maintenance requirements. This digital approach not only closes knowledge gaps but also reduces human error, duplication of work, and data loss.
Eliminating Inefficiencies and Reducing Maintenance Risks
Paper-based processes often cause delays due to extensive documentation and time spent moving between the shop floor and control rooms. Such practices result in data inaccuracies and missed maintenance opportunities, contributing to unplanned shutdowns and productivity losses. Innovapptive’s digital solution enhances data accuracy and optimizes resource allocation, reducing the risk of costly downtime.
Industry Insights: A recent study indicates that more than one-third of industrial accidents are caused by equipment failures stemming from inadequate maintenance practices. By providing real-time data access and reducing manual processes, Innovapptive’s asset dashboard not only streamlines operations but also bolsters workplace safety and regulatory compliance.
Request a Live Demo of Innovapptive’s Mobile Plant Maintenance Solution
To see Innovapptive’s mobile plant maintenance management solution in action, request a live demo today. From predictive maintenance to streamlined asset management, Innovapptive’s comprehensive mobile solutions are designed to meet the demands of modern plant operations and help companies stay ahead of industry challenges.
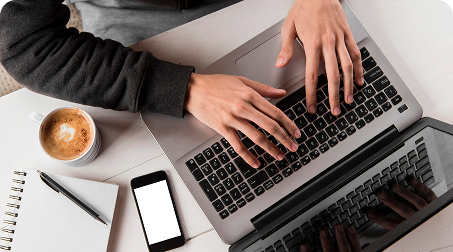
See It In Action
Schedule a personalized demo to see how our solutions can help your business thrive.
- 20-08-2025
Building the future of Industrial Operations with Innovapptive and AWS
Most manufacturers have already gone digital. Yet business outcomes haven’t moved in step. Many...
- 22-04-2025
The $3.6B Unlock: Solving the Chemical Industry’s Labor Crisis and EBITDA Pressure in One Move
“Constraints don’t slow innovation—they force it.”
- 21-04-2025
Chemical Industry's Margin Erosion: A Wake-Up Call for Operational Efficiency Amid China's Oversupply
The global chemical industry is facing mounting challenges, with revenue declines and shrinking...