Overcoming Costly Equipment Maintenance Challenges in the Mining Industry
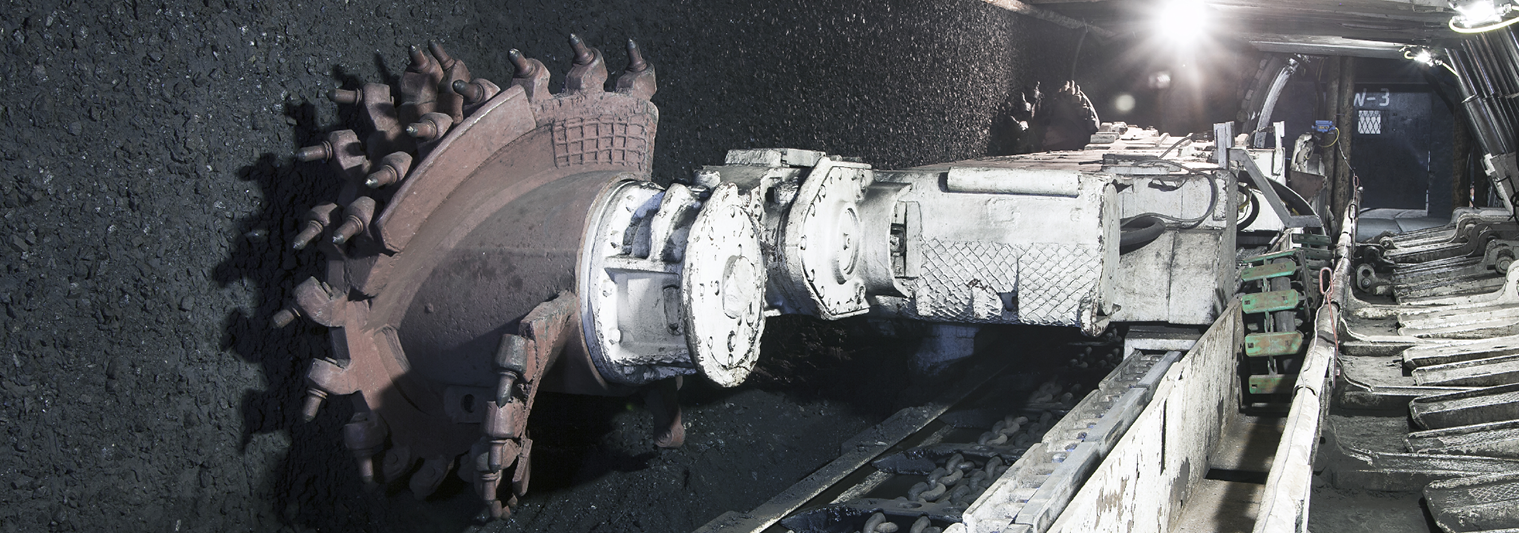
Mining is a highly complex industry. Its operations are intensive, risk-prone and unpredictable. The mining industry needs to overcome several challenges to remain competitive. This blog talks about the typical obstacles the mining industry faces and how a mobile plant maintenance (PM) solution can systematically mitigate these challenges.
Let’s decode these challenges and examine why you ought to consider an enterprise plant maintenance solution.
Equipment failures are disruptive and costly for high-value facilities: Maintenance forms one of the mining industry’s core operational pillars. A typical mining venture spends 35 to 50 percent of its annual operating budget on equipment maintenance and repairs. Despite having a preventive maintenance strategy in place, equipment failures are unpredictable and can come at any time, leading to production disruptions and heavy financial losses.
Resolution: Look for a mobile PM that lets your maintenance personnel electronically post notifications or work orders on the go, eliminating paper forms. The mobile PM should allow your staff to capture and share equipment information textually and visually (even 3D images) to help resolve these issues within the shortest time.
Satisfying regulatory requirements and ensuring safety standards: Safety is critical as miners operate in dangerous conditions. Figures from the U.S. Bureau of Labor Statistics show that American miners suffered 11.7 fatal injuries per 100,000 workers in 2017 (the latest number available). Most fatalities and injuries stem from contact with equipment.
Resolution: A good mobile PM solution should trigger automatic notifications if the equipment’s measuring point reaches the operational threshold limit to ensure safety compliance.
Track equipment at far-flung locations: When equipment breaks down at a remote site, it’s often hard for technicians to locate and repair it. Searching for it can be a herculean task, wasting several hours. There are also transportation costs to consider, impacting your revenues and budget.
Resolution: Invest in a solution that allows technicians to easily view equipment locations on an electronic, mobile device-accessible map, providing accurate directions to ensure speedy repairs.
Lack of connectivity at remote locations: Every minute counts in the mining industry. Mobile communications ensure that each minute is productive. However, mobile solutions need a signal or internet connectivity. Most of the world’s mining operations are in remote locations with little or no communications infrastructure. This can make mobile communications difficult, even impossible, posing a challenge for mobile PM solutions.
Resolution: Look for a PM solution that functions in online or offline modes so your remote workers can track and monitor work orders and notifications on the go, even at sites with limited or no connectivity.
Lack of planning accuracy: Operational transparency is essential for any business’s success. Planning and scheduling require timely, accurate information to minimize downtime and make the best use of labor and resources. Without this, maintenance and production managers and directors must rely on intuition, experience and even guesswork to plan and schedule critical activities and work orders. This inevitably results in inaccuracies and errors that can prolong planned downtime, lead to unplanned outages, hurt production and cut into revenues.
Resolution: The right mobile PM solution should allow you to receive continuous update on equipment health entered directly from technicians in the field. This eliminates guesswork and the need to rely on intuition. Instead, you’re given a clearer, up-to-date picture of actual conditions throughout your mine. Errors are reduced and problems can be addressed before they impact your operations and bottom line.
Incorrect data capture: Paper maintenance document processes are slow and lead to missing or incorrect data. Far too often, a critical document winds up sitting on someone’s desk awaiting approval while a problem in the field worsens. A document could also get lost or misfiled, meaning no one may be aware the problem exists, or workers are waiting for an approval that will never come.
The document could be badly designed, not allowing for entry of critical data needed for knowledgeable decision making. A document could have been poorly filled out, missing vital information, or the worker’s handwriting is so bad it’s illegible. Now no one can determine what problem has occurred because they can’t make out the form. Errors creep into your process.
All these scenarios result in negative consequences for your operations. Planning becomes difficult, decision making is delayed, and a potentially minor problem suddenly becomes a major one due to incorrect or delayed data capture and sharing.
Resolution: A proper mobile PM solution eliminates error, providing first-time digital data capture accuracy. Paper forms are eliminated. Workers in the field collect information while examining the equipment and immediately enter it electronically via hand-held devices. Planners, schedulers and managers can access this data in real time using a desktop dashboard. Problems can be quickly identified and addressed before they turn into unplanned downtime and reduced production.
Innovapptive’s Plant Maintenance Solution - mWorkOrder - offers the right mix of simplicity, functionality and scalability to meet your unique business needs within your budget. This robust solution optimizes your maintenance process, digitally connecting far-flung workers in the field to management in the office, enabling more effective communications and collaboration, quicker and more accurate identification of issues, more knowledgeable decision making, and faster responses to problems.
mWorkOrder is a proven solution that has helped mining companies of all sizes improve their maintenance operations and bottom line. To demo Innovapptive’s mWorkOrder solution, click here. You can also speak with an Innovapptive’s Solution Expert via phone at (713) 275-1804 or email at sales@innovapptive.com.
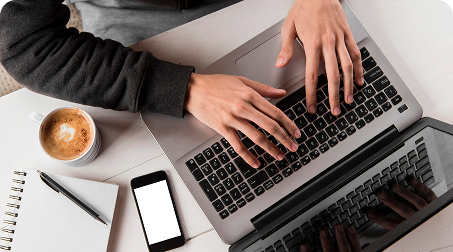
See It In Action
Schedule a personalized demo to see how our solutions can help your business thrive.
- 22-04-2025
The $3.6B Unlock: Solving the Chemical Industry’s Labor Crisis and EBITDA Pressure in One Move
“Constraints don’t slow innovation—they force it.”
- 21-04-2025
Chemical Industry's Margin Erosion: A Wake-Up Call for Operational Efficiency Amid China's Oversupply
The global chemical industry is facing mounting challenges, with revenue declines and shrinking...
- 21-04-2025
Why Wrench Time Isn’t Improving: The Hidden Costs of Traditional Maintenance Scheduling
For years, industrial leaders have relied on a common but flawed assumption: "Better planning and...