When You Should Consider a Condition-Based Maintenance Approach
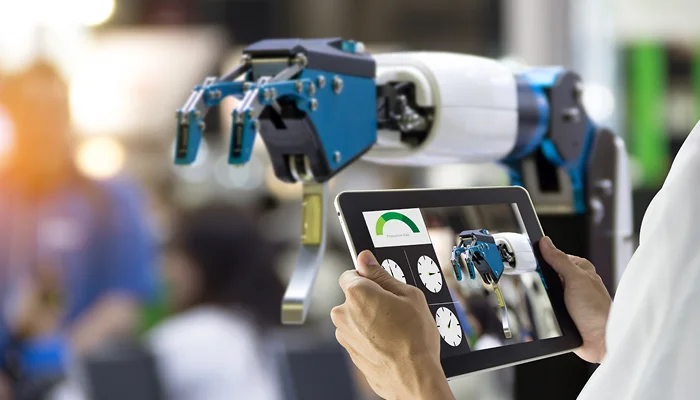
Traditional maintenance strategies like time-based maintenance or risk-based maintenance often lead to unnecessary downtime and inflated costs. This is where condition-based maintenance (CBM) becomes a game-changer. By monitoring the condition of equipment in real time, CBM ensures that maintenance occurs only when necessary, leading to better asset performance and cost savings.
What is Condition-Based Maintenance?
Condition-based maintenance is a proactive maintenance strategy that uses real-time data and monitoring tools to assess the condition of assets. Sensors and diagnostic tools continuously measure various equipment parameters, such as temperature, vibration, and pressure. This data helps determine when maintenance should be performed, preventing unexpected failures and extending the asset's lifecycle.
By monitoring the actual condition of equipment, condition-based maintenance ensures that maintenance activities are only conducted when there are signs of degradation, rather than on a pre-determined schedule.
Condition-Based Maintenance vs. Predictive Maintenance
Both condition-based maintenance and predictive maintenance are strategies that help avoid unnecessary maintenance activities. However, the two approaches differ in their techniques and scope:
Condition-Based Maintenance vs Predictive Maintenance
While condition-based maintenance focuses on immediate equipment condition through sensors and real-time monitoring, predictive maintenance uses advanced data analytics, machine learning, and historical data to predict future failures. Both approaches are aimed at increasing operational efficiency, but predictive maintenance can help anticipate issues before they occur, whereas condition-based maintenance is triggered only when equipment performance declines.
Understanding the difference between condition-based maintenance vs predictive maintenance can help companies choose the most effective approach depending on their operational needs.
Benefits of Condition-Based Maintenance
Implementing condition-based maintenance comes with a host of benefits. Here are the key advantages of condition-based maintenance:
Condition-Based Maintenance Benefits
- Reduced Downtime: By addressing issues before they lead to equipment failure, condition-based maintenance minimizes unplanned downtime.
- Cost Savings: Since maintenance is performed only when needed, condition maintenance reduces unnecessary interventions, saving on labor, parts, and material costs.
- Improved Asset Lifespan: Real-time monitoring and proactive maintenance help keep equipment running efficiently for longer.
- Increased Safety: Identifying potential failures before they happen reduces the risk of accidents or hazardous situations.
However, there are also disadvantages of condition-based maintenance, including high initial setup costs and the need for ongoing monitoring, training, and system integration.
Types of Condition-Based Maintenance
Several methods are used to implement condition-based maintenance. These methods help monitor the health of equipment to ensure that maintenance is performed only when needed. Here are the types of condition-based maintenance commonly used in industries today:
Vibration Analysis
Vibration analysis is used to monitor equipment like motors and pumps. By detecting changes in vibration patterns, it can identify issues such as imbalances, misalignment, or bearing failure.
IR Thermography
Thermal imaging detects abnormal heat levels in electrical components or mechanical equipment, which helps in identifying potential problems such as overheating or faulty insulation.
Ultrasonic Analysis
Ultrasonic sound waves are used to detect leaks in pressurized systems or identify mechanical failures in rotating equipment like compressors.
Oil Analysis
Oil analysis helps monitor the health of lubricants and determines the presence of contaminants, wear particles, or fluid breakdown that might indicate an issue with equipment.
Electrical Analysis
Fluctuations in electrical parameters can cause equipment failure. Electrical analysis helps monitor and stabilize voltage and current to avoid malfunctions.
Pressure Analysis
Pressure monitoring in systems that transport fluids or gases helps identify leaks, blockages, or abnormal conditions that could lead to a failure.
What is Condition-Based Monitoring Maintenance?
Condition-based monitoring maintenance is a specific application of condition-based maintenance that focuses on the continuous monitoring of an asset's performance through sensors and data analytics. It enables operators to assess the condition of equipment in real-time, thereby reducing the need for manual inspections and enabling timely intervention when issues are detected.
The key advantage of condition-based monitoring maintenance is that it allows for continuous performance tracking, ensuring that any potential problems are detected before they escalate into major failures.
Condition-Based Maintenance Systems
A condition-based maintenance system integrates various monitoring tools and sensors to collect real-time data from equipment. This data is then analyzed to determine when maintenance is needed. These systems often include software for asset management, alert systems, and predictive tools to help maintenance teams take timely action.
The integration of condition-based maintenance software ensures that data flows seamlessly across the organization, facilitating collaboration among different stakeholders, and improving decision-making.
Condition-Based Maintenance Strategy
Implementing a condition-based maintenance strategy requires careful planning and integration with existing systems. Here's how to build a successful strategy:
- Identify Critical Assets: Focus on equipment that is most critical to operations and has the highest impact when it fails.
- Select Appropriate Monitoring Tools: Choose sensors and diagnostic tools that align with the needs of the asset and the maintenance goals.
- Integrate with EAM Systems: Use condition-based maintenance software to link real-time data with an asset management system, improving decision-making.
- Monitor and Analyze Data: Continuously track the asset’s condition and look for any anomalies that might indicate a problem.
Condition-Based Maintenance Examples
Several industries use condition-based maintenance strategies to improve asset management. Here are a few condition-based maintenance examples:
- Manufacturing: Vibration and thermal analysis are commonly used to monitor motors, pumps, and bearings in factories.
- Oil & Gas: Pressure and ultrasonic analysis are used to monitor pipelines and prevent leaks.
- Automotive: Oil and vibration analysis are used to ensure the optimal performance of critical vehicle components.
By leveraging condition-based maintenance software and real-time monitoring tools like Mobile EAM solutions, industries can enhance asset reliability and optimize maintenance schedules.
Condition-Based Maintenance Software
To effectively manage condition-based maintenance, companies rely on specialized condition-based maintenance software. These tools collect real-time data from sensors, provide alerts when maintenance is needed, and offer insights into asset performance, helping teams schedule maintenance activities more efficiently.
Challenges of Condition-Based Maintenance
While condition-based maintenance offers many advantages, there are some disadvantages of condition-based maintenance:
- High Initial Costs: Setting up the necessary sensors, equipment, and software can be expensive.
- Skill Requirements: Proper training is required to interpret sensor data accurately.
- Data Management: Ensuring data accuracy and proper integration across systems can be a challenge.
Conclusion
In conclusion, condition-based maintenance is a powerful strategy that helps industries optimize asset performance, reduce downtime, and improve cost-efficiency. By implementing the right condition-based maintenance system and monitoring tools, businesses can stay ahead of potential issues, improve safety, and increase the lifespan of critical assets.
Whether you're looking to implement a condition-based maintenance strategy or explore the differences between condition-based maintenance vs predictive maintenance, understanding these practices will help you make informed decisions for your business.
Get Started with Condition-Based Maintenance Today
Implementing a condition-based maintenance strategy can significantly boost your asset reliability, reduce downtime, and optimize maintenance costs. At Innovapptive, we provide Mobile EAM solutions that help you leverage real-time data for smarter, more efficient maintenance management.
Ready to transform your maintenance approach and unlock the full potential of your equipment? Contact us today to learn how Innovapptive can help you integrate condition-based maintenance seamlessly into your operations and take your asset management to the next level.
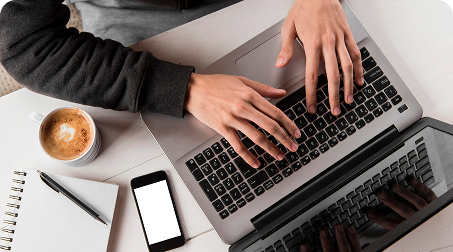
See It In Action
Schedule a personalized demo to see how our solutions can help your business thrive.
- 20-08-2025
Building the future of Industrial Operations with Innovapptive and AWS
Most manufacturers have already gone digital. Yet business outcomes haven’t moved in step. Many...
- 22-04-2025
The $3.6B Unlock: Solving the Chemical Industry’s Labor Crisis and EBITDA Pressure in One Move
“Constraints don’t slow innovation—they force it.”
- 21-04-2025
Chemical Industry's Margin Erosion: A Wake-Up Call for Operational Efficiency Amid China's Oversupply
The global chemical industry is facing mounting challenges, with revenue declines and shrinking...