Three Ways Innnovapptive’s Connected Worker Platform Transforms Maintenance and Operations
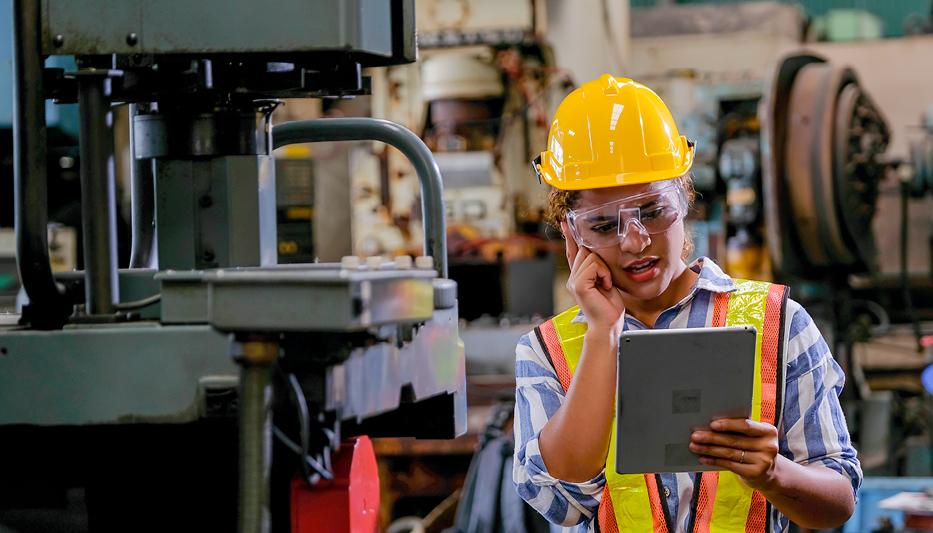
Smart machines are conquering factory floors in Industry 4.0 but unpredictable situations in manufacturing still need human intervention from maintenance technicians, making them irreplaceable resources.
Unfortunately, frontline workers haven’t been equipped with technology advancements they need and still use conventional data practices. Error-prone paper forms and information silos jeopardize worker efficiency and safety.
Innovapptive’s Connected Worker Platform disrupts this status quo and creates safer and more efficient workplaces. It bridges the gap between factory floors and the back-office to establish real-time visual communication.
Here are three ways our platform helps organizations tap into the full potential of their frontline workforce.
Go mobile and beyond
Frontline workers fumble with paper forms and checklists while executing mission-critical tasks. A Service Council study found 46 % of field technicians claimed that paperwork and administrative tasks were the worst part of their day-to-day job. Companies use ERP systems such as SAP to digitalize data but still rely on paper in the field.
Some ERP providers offer web-based or hybrid mobile applications that are only as good as paper forms and fail to leverage the full power of mobile.. Almost half of frontline workers expect workplace technologies to perform just like their personal technology.
The global enterprise mobility market accounted for $206.13 billion in 2017 and is expected to reach $1225.78 billion by 2026 growing at a CAGR of 21.9% during the forecast period.
-Business Insider
We found, from our experience working with global companies, that poor network availability in remote locations, complex workflows and security risks were key factors triggering resistance to change.
That’s why we built off-the-shelf mobile solutions for asset-intensive companies. The intuitive UI/UX of our solutions makes them usable, accessible, desirable and findable. These solutions can be integrated into wearables including smart glasses and smartwatches, to enable voice-based, hands-free operations on the factory floor.
Our encryption methods underpin the security and integrity of data flowing through the solutions. These solutions work in both offline and online conditions, eliminating the need for extensive Wi-Fi networks. Field technicians are able to focus on their work and don’t have to worry about having an internet connection.
No-code/Low-code customization:
The customization of enterprise mobile solutions is critical and challenging. Business processes, workflows and regulations often change in manufacturing plants. Relying on vendors for every tiny change increases costs for a company. On the other hand, maintaining in-house IT teams can be a costly alternative..
Wouldn’t it be awesome if an engineering manager himself customized the solution to reflect process changes?
Innovapptive pioneered the no-code/low-code Connected Worker space with its proprietary Rapid Application Configuration Engine (RACE™). RACE™ enables managers and IT teams to customize the solutions within minutes. This ensures field technicians receive updated information and follow the latest regulatory standards to achieve sustainable growth.
An ecosystem of connected operations
Conventional practices create silos that lead to communication breakdowns across an organization. A Deloitte study found that more than a third of industry leaders regarded organizational silos as one of the top three challenges to setting an Industry 4.0 strategy.
Innovapptive is solving this problem by connecting different frontline teams, including maintenance, engineering and inventory, to enable the free flow of information across the organization.
We offer a mobile work order management solution, mobile inventory management solution, mobile asset management solution, digital operator rounds and digital work instructions solutions as part of our robust Connected Worker Platform.. These mobile solutions are integrated with ERP systems such as SAP, connecting field workers with the back-office. This creates an ecosystem of connected operations where a maintenance planner prioritizes work orders based on real-time rounds data, a technician knows the availability of spare parts and an expert helps him with visual guidance to work faster and safer.
This ecosystem breaks information silos. If a technician working in a company’s plant in North America learns a new thing about a process, he can update the information via the mobile solution. This quickly gets synced with the ERP system and technicians in other plants across the world can access the information. This improves the efficiency and productivity of not just that one technician but technicians at all plants, driving organizational growth.
Want to learn more?
We are always happy to help you. Book a live, custom demo here. Call 1-844-464-6668 to reach out to our experts.
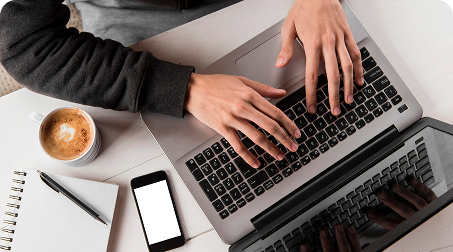
See It In Action
Schedule a personalized demo to see how our solutions can help your business thrive.
- 20-08-2025
Building the future of Industrial Operations with Innovapptive and AWS
Most manufacturers have already gone digital. Yet business outcomes haven’t moved in step. Many...
- 22-04-2025
The $3.6B Unlock: Solving the Chemical Industry’s Labor Crisis and EBITDA Pressure in One Move
“Constraints don’t slow innovation—they force it.”
- 21-04-2025
Chemical Industry's Margin Erosion: A Wake-Up Call for Operational Efficiency Amid China's Oversupply
The global chemical industry is facing mounting challenges, with revenue declines and shrinking...