What is a Connected Worker?
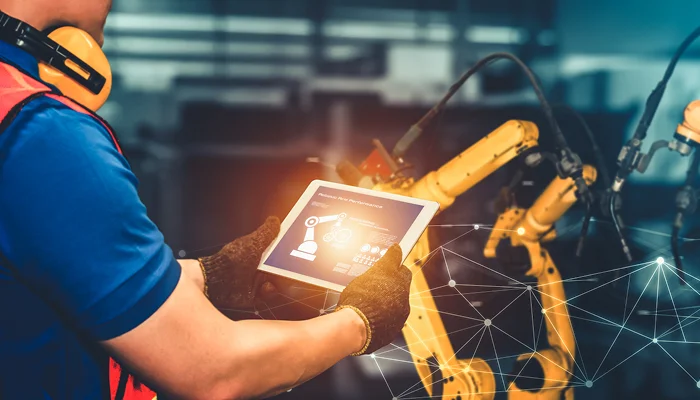
Industrial operations are undergoing rapid digital transformation, yet a critical gap persists: frontline workers often lack access to the advanced tools and technologies available to back-office staff. While systems like Enterprise Resource Planning (ERP), Enterprise Asset Management (EAM), and Customer Relationship Management (CRM) have enhanced productivity and decision-making in industrial organizations, frontline workers—such as maintenance technicians, warehouse operators, and field engineers—are often left using outdated, manual processes.
Connected Worker solutions bridge this divide by empowering frontline workers with mobile tools, wearables, and digital technologies that integrate them seamlessly into the organization’s digital ecosystem. These solutions provide real-time access to the same data and systems that have revolutionized industrial back-office operations.
The Digital Divide in Industrial Transformation
The Fourth Industrial Revolution (Industry 4.0) has introduced groundbreaking technologies such as robotics, IIoT (Industrial Internet of Things), and artificial intelligence to asset-intensive industries. These advancements have enabled back-office employees to work remotely and collaborate effectively using tools like video conferencing and real-time dashboards. However, frontline workers often remain disconnected from these advancements.
For example, field maintenance technicians frequently travel to remote locations with paper-based checklists, work orders, and manuals. After completing their tasks, they return to the office to manually enter their findings, creating delays, inefficiencies, and the risk of human error. These challenges include:
- Data inaccuracies due to manual input.
- Inefficiencies caused by duplicate work and redundant processes.
- Reduced wrench time as technicians wait for instructions, spare parts, or work orders.
- Increased inventory carrying costs due to siloed data.
- Delays in decision-making from outdated or incomplete asset information.
- Compliance risks due to outdated inspection forms and inconsistent documentation.
This disconnect not only hampers productivity but also increases operational costs, making it harder for organizations to compete in today’s fast-paced industrial landscape.
What is a Connected Worker Solution?
A Connected Worker solution integrates frontline workers into the digital ecosystem using mobile applications, wearables, and technologies such as augmented reality (AR), IoT sensors, and GPS. These tools replace outdated manual processes with real-time data access, enabling workers to contribute and interact with enterprise systems like ERP, EAM, or CRM platforms.
Core Features of Connected Worker Solutions
1. Mobile Accessibility:
Workers can view work orders, access manuals, and update task statuses in real-time from any location.
2. Wearables:
Devices like smart glasses and rugged tablets allow hands-free operation, enhancing safety and efficiency.
3. Augmented Reality:
Technicians can use AR for visual instructions, remote support, and troubleshooting.
4. Digital Workflows:
Paper-based checklists are replaced with intuitive digital forms, reducing errors and improving compliance.
5. Real-Time Data Synchronization:
Information is instantly uploaded to enterprise systems, ensuring all stakeholders have access to accurate, up-to-date data.
6. Predictive Analytics Integration:
IoT-enabled tools help prevent equipment failures through proactive maintenance insights.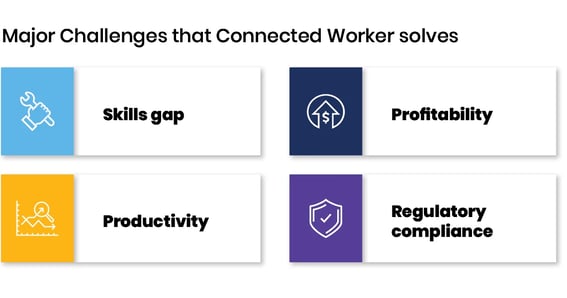
Benefits of Connected Worker Solutions
Connected Worker solutions revolutionize industrial operations by addressing key pain points and delivering measurable outcomes.
1. Enhanced Productivity
Frontline workers can access real-time instructions, check spare part availability, and complete tasks faster with mobile tools. For instance:
- Technicians can use AR for visual guidance, reducing repair times by up to 30%.
- Warehouse workers can perform inventory checks using barcode scanning, eliminating manual errors.
2. Improved Data Accuracy
Real-time data entry minimizes the risk of human error and ensures that enterprise systems reflect the most current information.
3. Reduced Downtime
With IoT-enabled sensors and predictive maintenance insights, technicians can proactively address issues before they escalate.
4. Better Compliance Management
Digital forms and workflows enable compliance managers to update inspection forms in line with regulatory changes, avoiding penalties and ensuring operational safety.
5. Cost Savings
Organizations can reduce inventory carrying costs, minimize rework, and improve resource allocation, resulting in significant financial benefits.
How Connected Worker Solutions Improve Maintenance and Productivity
The integration of Connected Worker solutions transforms maintenance, operations, and overall business performance:
- Maintenance Excellence: Field technicians receive instant support via AR, enabling them to resolve issues with precision.
- Streamlined Inventory Management: Warehouse teams can manage stock levels in real-time, reducing overstock and shortages.
- Collaboration and Knowledge Sharing: Remote support tools and AR enable workers to collaborate with experts anywhere in the world.
- Real-Time Decision-Making: Accurate, up-to-date data from the field empowers back-office staff to make informed decisions that enhance efficiency.
For example, a leading manufacturing company reduced downtime by 20% and increased technician productivity by 35% after implementing a Connected Worker solution.
Discover the Impact of Innovapptive’s Connected Worker Platform
A leading manufacturer revolutionized its operations, significantly reducing downtime and improving Mean Time to Repair (MTTR). Learn more in the case study.
Overcoming Challenges in Connected Worker Solution Implementation.
Despite the benefits, some organizations face challenges in adopting Connected Worker solutions, such as:
1. Integration with Legacy Systems
Innovapptive’s modular solutions seamlessly integrate with ERP platforms like SAP and IBM Maximo, ensuring smooth adoption.
2. Employee Resistance
User-friendly interfaces and robust training programs make the transition simple and intuitive for frontline workers.
3. Initial Costs
While upfront investment may seem high, the long-term ROI—through reduced downtime, improved productivity, and lower operational costs—far outweighs initial expenses.
Why Choose Innovapptive for Connected Worker Solutions?
Innovapptive stands as a pioneer in Connected Worker technology, offering end-to-end solutions that empower frontline teams and streamline industrial operations.
Key Advantages of Innovapptive's Solutions:
- Seamless Integration: Real-time data synchronization eliminates silos and connects frontline and back-office operations.
- Advanced Features: Cutting-edge tools like AR, wearables, and IoT integration deliver superior functionality.
- Tailored Solutions: Customizable modules meet the specific needs of industries, from manufacturing to utilities.
- Proven Results: With nearly a decade of experience, Innovapptive helps organizations achieve measurable outcomes like improved productivity, reduced costs, and enhanced compliance.
With Innovapptive, you can bridge the gap between your frontline and back-office teams, completing your digital transformation journey and staying competitive in the Industry 4.0 era.
Take the First Step Towards Digital Transformation
Are you ready to bridge the digital divide in your operations? Innovapptive’s Connected Worker solutions can help you enhance productivity, reduce costs, and ensure compliance. Schedule a free demo today.
Frequently Asked Questions (FAQs)
1. What is a Connected Worker, and how do Connected Worker solutions improve industrial operations?
A Connected Worker is an employee who uses digital tools to access real-time data, collaborate remotely, and complete tasks efficiently. Connected Worker solutions improve industrial operations by enhancing communication, reducing downtime, and optimizing workflows.
2. How do Connected Worker solutions bridge the digital gap between frontline and back-office employees?
These solutions enable seamless data sharing, mobile access to work orders, and instant collaboration, ensuring alignment between frontline workers and back-office teams.
3. How do Connected Worker solutions improve productivity and efficiency?
They eliminate manual paperwork, automate routine tasks, provide real-time insights, and streamline workflows, leading to faster decision-making and improved efficiency.
4. How does real-time data access benefit frontline workers?
Real-time data access allows workers to make informed decisions, reduces errors, improves response times, and enhances overall operational safety and performance.
5. How do Connected Worker solutions integrate with ERP, EAM, and CRM systems?
They connect with ERP, EAM, and CRM systems to provide a unified data flow, ensuring accurate inventory tracking, work order management, and customer insights across all operations.
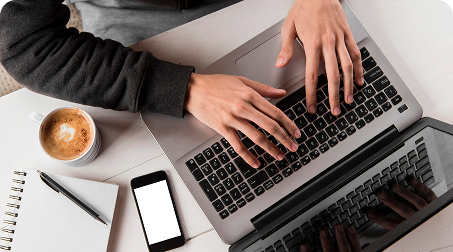
See It In Action
Schedule a personalized demo to see how our solutions can help your business thrive.
- 20-08-2025
Building the future of Industrial Operations with Innovapptive and AWS
Most manufacturers have already gone digital. Yet business outcomes haven’t moved in step. Many...
- 22-04-2025
The $3.6B Unlock: Solving the Chemical Industry’s Labor Crisis and EBITDA Pressure in One Move
“Constraints don’t slow innovation—they force it.”
- 21-04-2025
Chemical Industry's Margin Erosion: A Wake-Up Call for Operational Efficiency Amid China's Oversupply
The global chemical industry is facing mounting challenges, with revenue declines and shrinking...