The Impact of Artificial Intelligence & Machine Learning (AI/ML) on Operations
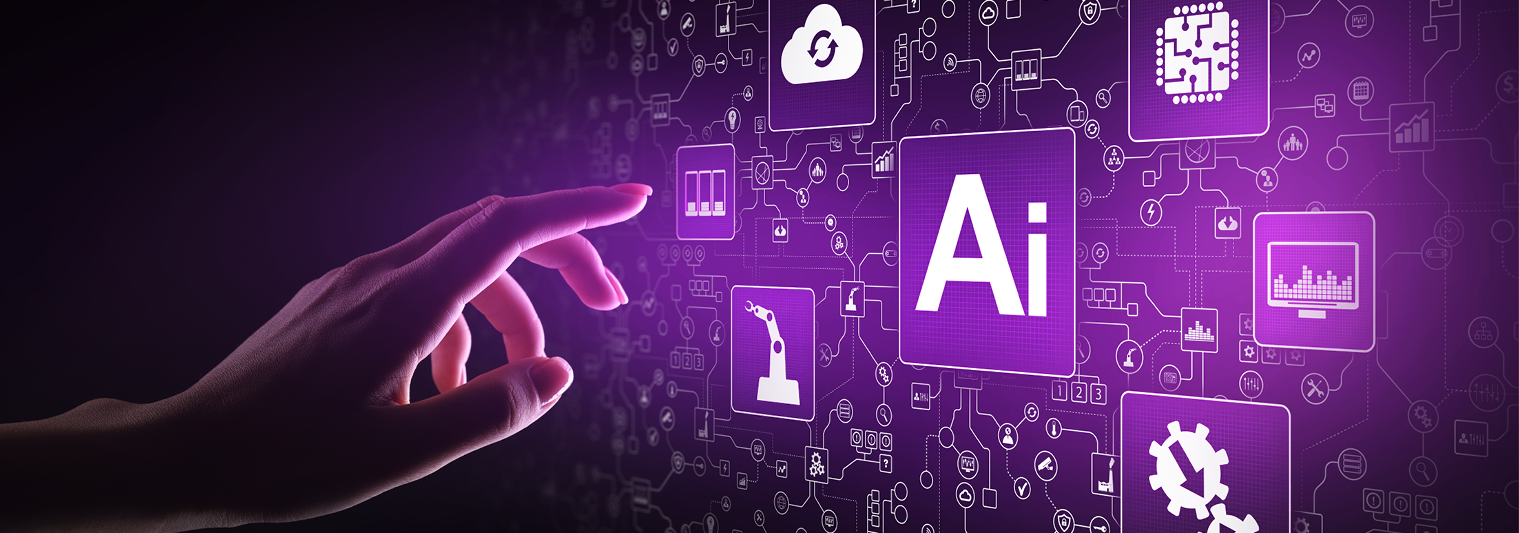
Hollywood has put out lots of movies about artificial intelligence (AI). But AI is no longer science fiction; it’s here now. And for those companies seeking digital transformation, AI and ML represent the pinnacle of that quest.
You may be one of these companies. And you may be wondering what’s the best path to reach that goal. You can’t just go to the AI store, purchase a HAL-9000, a WALL-E or Robby the Robot and put them to use tomorrow. There are other small steps to take first. In this blog, we’ll discuss the role of AI across operations such as maintenance and repair and illustrate how Innovapptive, a mobile-first operations platform serves as your first step towards this destination.
Chatbots and AI are disrupting the way conversations happen and are the current rage in most asset-intensive industries. They enable service engineers and technicians in the field to instantly extract information about the equipment that may need repair or replacement. AI and machine learning can transform massive amounts of sensor data into meaningful insights that makes maintenance processes agile, efficient and cost-effective.
Let’s take a case in the manufacturing industry. Say a sensor or a connected device is fitted to a pipeline or a transformer that measures and tracks the health and performance of the asset. When this equipment encounters a potential problem, it pools the relevant data (equipment type, measurable characteristics, severity of the problem) and alerts the back-office to take action. This could be planning a preventative inspection when the problem doesn’t require immediate attention, or immediately dispatching a work order to the nearest technician when it does. The technician on the way to the site has all this information readily available on his/her mobile, making it easier to fix the problem quickly.
Once the technician arrives, he/she can strike a conversation with the chatbot (integrated with the equipment sensor) asking a series of questions like:
- How was the performance of my equipment in the past few weeks?
- Did you notice any unusual activity in my equipment?
- Are the spare parts in stock?
- Is there any potential risk to the equipment, people or the environment?
The AI-powered chatbot filters the collated data and triggers the right results on the screen, cutting the technician’s time to manually search information. This is an innovative way of making maintenance tasks more effective. These chatbots are more like smart advisors and provide value far above the personal assistants like Amazon’s Echo system or Apple’s Siri, which are more applicable in B2C contexts.
Instead of just predicting the equipment behavior, what if chatbots could simulate human actions - create work orders and raise notifications on your behalf? What if you can ask chatbot the following questions, prompting it to act instantly:
- Create a work order on <equipment number> of <plant type> with criticality <nature of criticality (severe, normal, emergency)>?
- List out the notifications generated on <date> and <time>?
- List out the work orders created by <technician’s id> on <date> and <time>?
Let’s take a practical scenario. Let’s assume a motor’s bearing valve needs to be repaired on site. The engineer in charge of the site will ask the chatbot to create a work order and assign it to the nearest technician. The chatbot will automatically trigger a work order with work order number, date, severity, equipment location (using GPS) and more and assign it to the nearest technician.
The technician then logs into the application and asks the chatbot to list out the assigned work orders for a specific date. The chatbot instantly filters the list of assigned work orders, based on the severity, equipment type and resolution date. After the technician fixes the asset within the timeframe, a chatbot automatically triggers a notification to the field engineer. This way, a chatbot can trigger a two-way communication channel or even a multi-communication network, paving way for a connected workforce ecosystem.
These are just some of the high-level breakthroughs AI offers. If you’re still stuck in a paper-based process and want to explore this exciting world, Innovapptive offers a solid digital transformation foundation you can build upon. The first step on the road to AI is mobilization.
Mobilizing your maintenance activities via smartphones, scanners and wearables gives your workforce the ability to be productive anywhere, anytime throughout your enterprise. It electronically connects your field employees with management via back-office systems, improving communication and collaboration by removing information silos. Finally, mobility delivers accurate, high-value data you can see in real time to make more informed decisions.
To learn how to optimize your maintenance digital transformation and mobility, schedule a free demo today or call 844-464-6668
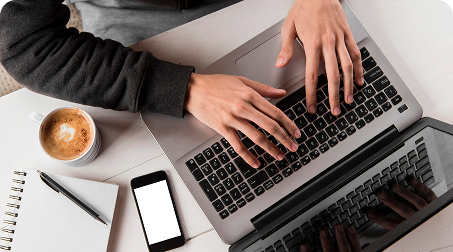
See It In Action
Schedule a personalized demo to see how our solutions can help your business thrive.
- 22-04-2025
The $3.6B Unlock: Solving the Chemical Industry’s Labor Crisis and EBITDA Pressure in One Move
“Constraints don’t slow innovation—they force it.”
- 21-04-2025
Chemical Industry's Margin Erosion: A Wake-Up Call for Operational Efficiency Amid China's Oversupply
The global chemical industry is facing mounting challenges, with revenue declines and shrinking...
- 21-04-2025
Why Wrench Time Isn’t Improving: The Hidden Costs of Traditional Maintenance Scheduling
For years, industrial leaders have relied on a common but flawed assumption: "Better planning and...